The soul of the music box lies in the comb, as its material, thickness, shape, and processing methods all influence the final sound quality produced during playback.
This article will take you deeper into the connection between the melodic features of music boxes and the design of the damper, as well as our experimental process dedicated to optimizing the durability and sound quality of the comb. From the development of the N20 music box with twenty notes in 2018 to the N40 music box with forty notes developed in 2023, the design of the comb has evolved to meet the expectations of professional musicians and top music box collectors.
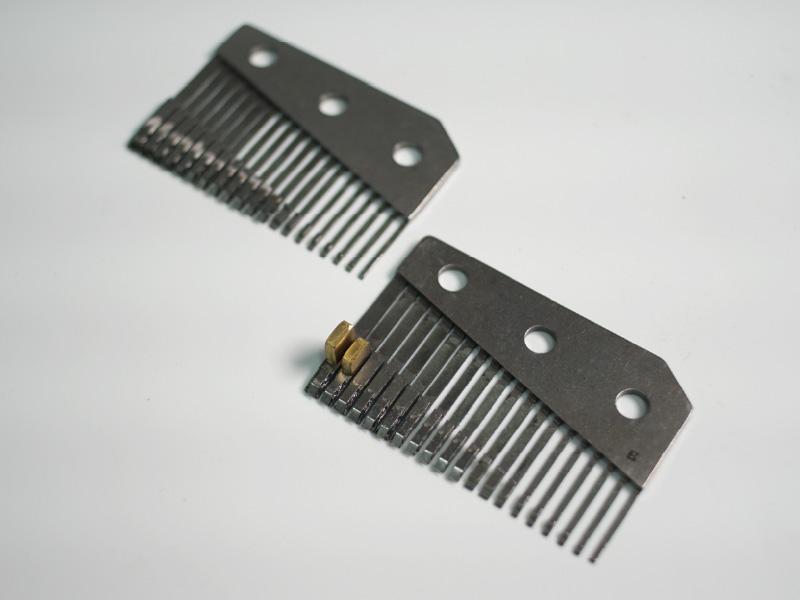