Manufacturing Process of the Muro Box-N40’sWeighted and Printed Circuit Board (PCB)
Muro Box-N40 Update #17
Hi Everyone,
This is Muro Box’s inventor, Dr. Chen-Hsiang Feng. The following is our latest N40 update’s summary:
▴The N40’s printed circuit boards (PCB) started to be manufactured on March 12, 2024. We visited the production line at Mighty Net to document the production process.
▴Due to insufficient weight on the vibration plate for the lower notes, we have redesigned the tuning weight and recorded how it is produced.
▴N40 Shipping plan is explained.
Visiting Mighty Net
The printed circuit boards (PCB) for the N40 were scheduled to enter production at the Mighty Net assembly line in Xinfeng Township, Hsinchu County on March 12th, 2024. We took advantage of this opportunity for the entire company to visit the site together, observing and documenting the production process.
In a stark contrast to many app functions of our product, one of the design philosophies of Muro Box is to “not look like an electronic product at all”. Therefore, the PCB is not visible from the outside, and even the power indicator light is intentionally designed to be very inconspicuous.
We differentiate between generations of products using the colors of the printed circuit board. Starting from the first-generation Muro Box-N20 model using black, we have also used green and red. In order to match with the Muro Box-N40 Sublime’s pure brass color scheme, we opted for yellow, echoing the brass color scheme of it and highlighting the traditional color symbolism of “nobility”.
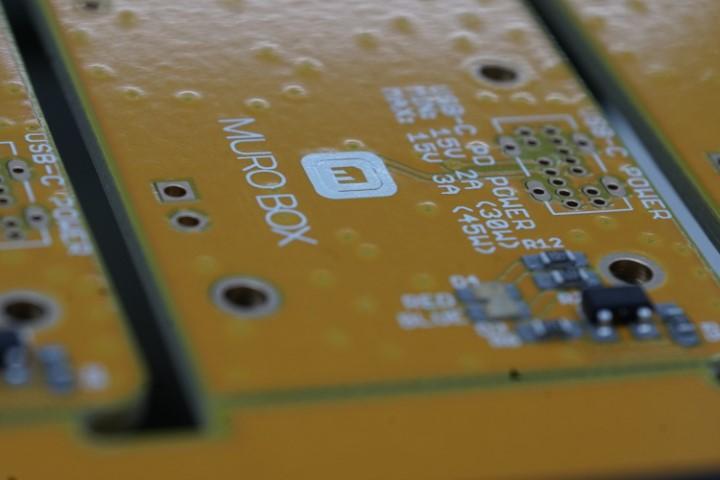
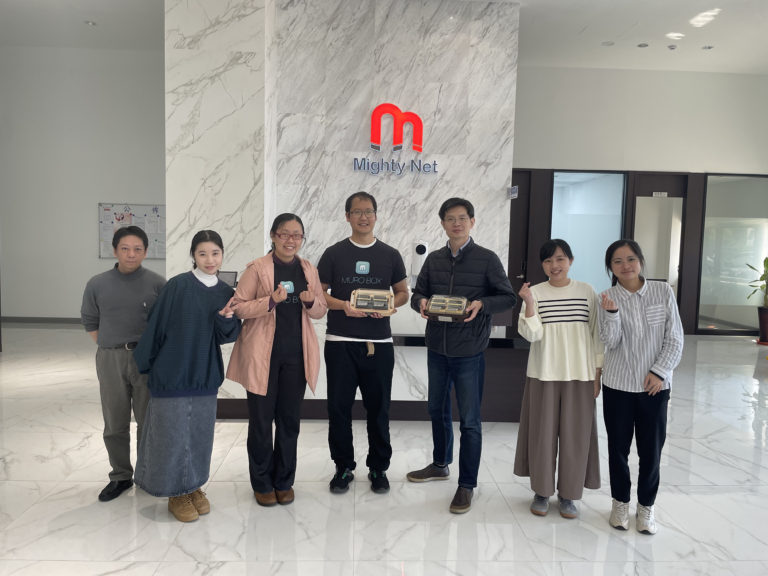
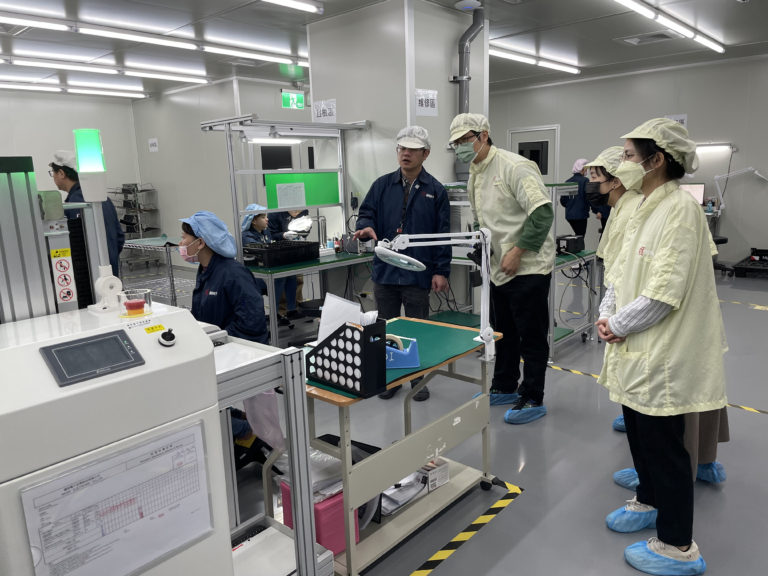
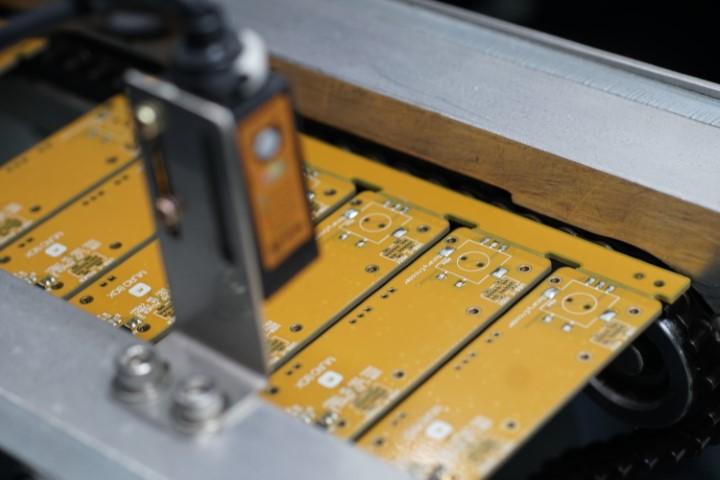
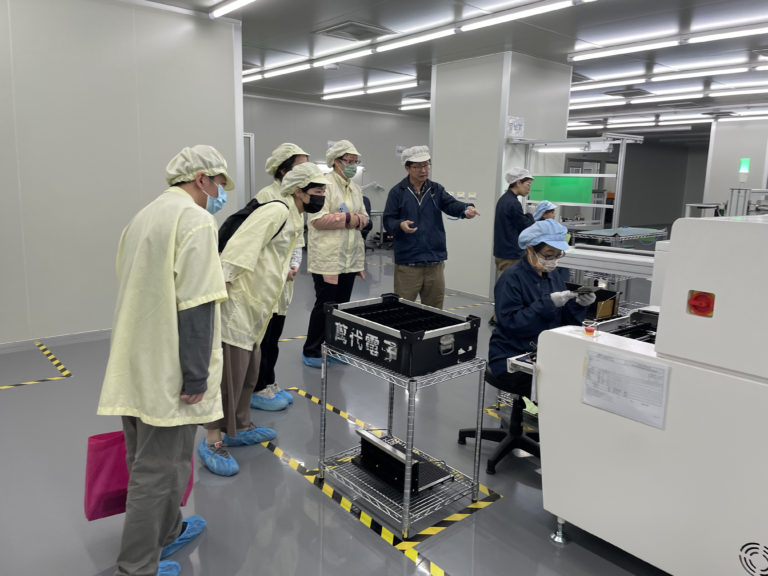

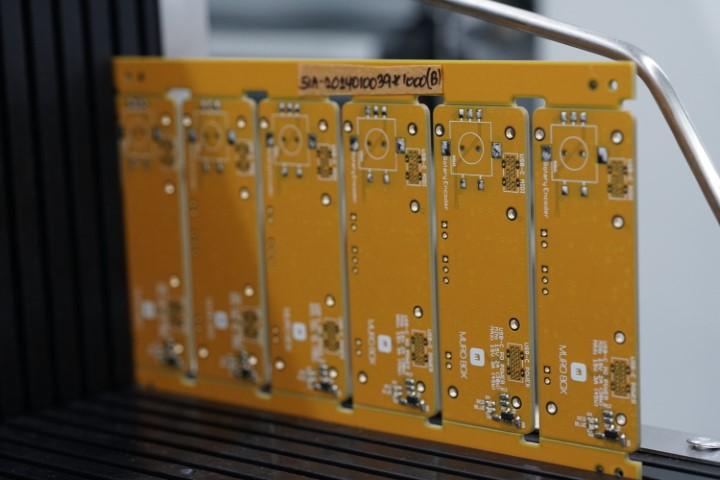
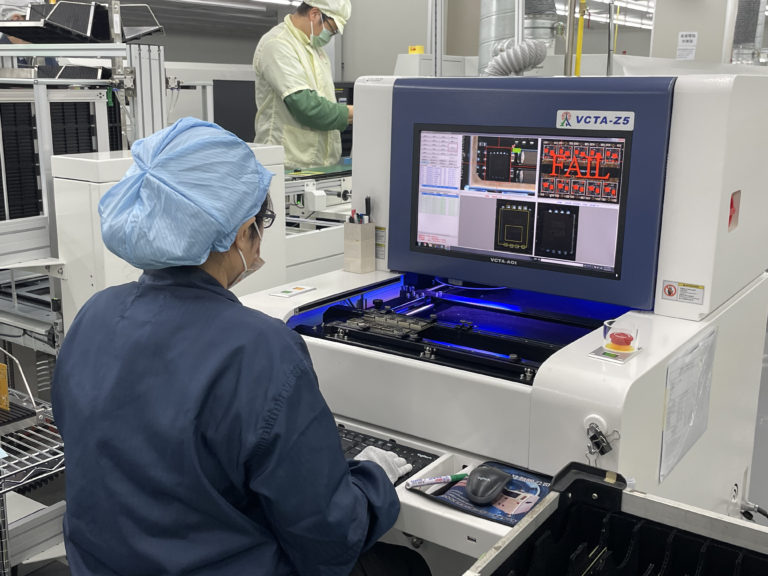
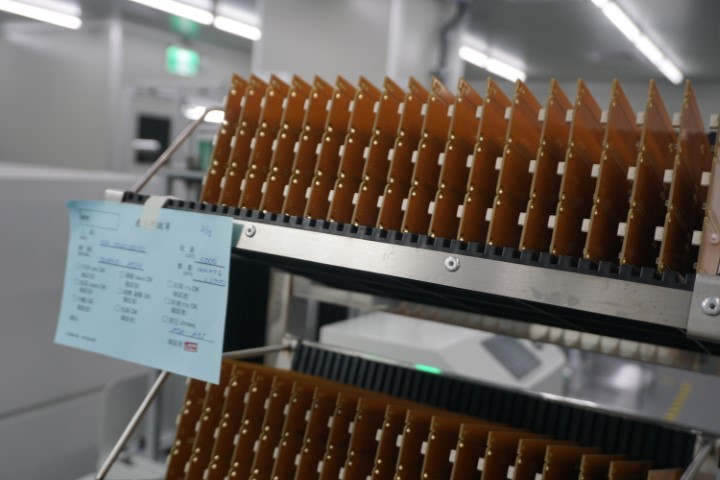
▲The PCBs for the N40 were manufactured by Mighty Net. Our team also visited the production facility on the scheduled manufacturing date to explore the working environment, including the precision instruments and the activities of the factory personnel.
Call of N40 Melodies Has Successfully Concluded
Thank you all for your participation. The contest has ended successfully, and we even received enthusiastic submissions from one individual with dozens of songs. However, we regret to inform you that in order to give more artists a chance to be featured in the Muro Box-N40 Official Playlist, we have limited the selection to one song per author.
Currently, we are in the process of compiling and evaluating the songs. The next N40 update will share the latest official song list for the N40. Please stay tuned!
N40 Production Status
Shipping Risks:
As previously mentioned, our goal is to begin shipping to customers starting from the first week of April. Currently, the challenge lies in the gradual arrival of various components. However, the absence of any single component could impede the shipping process. We will make every effort to ensure that all components arrive on time. Currently, the two components with higher risks are the resonance box and the vibration plate.
Resonating Box’ Risk:
The resonating box itself was designed relatively late in the process, so the supplier couldn’t prepare materials in time. We have coordinated with the supplier to ship in small batches, and our goal of shipping in the first week of April is still feasible.
Vibration Plate’s Risk:
Our task with the vibration plate is to add additional brass tuning weights to the two lowest tones of the comb. This is because the lower tones of our comb lack sufficient weight. If additional weight is not added, directly tuning them will cause the base of the comb teeth to become thin, resulting in insufficient strength, leading to easy deformation of the comb (resulting in a higher defect rate), and the volume of the lower tones will also be insufficient (resulting in quieter sound).
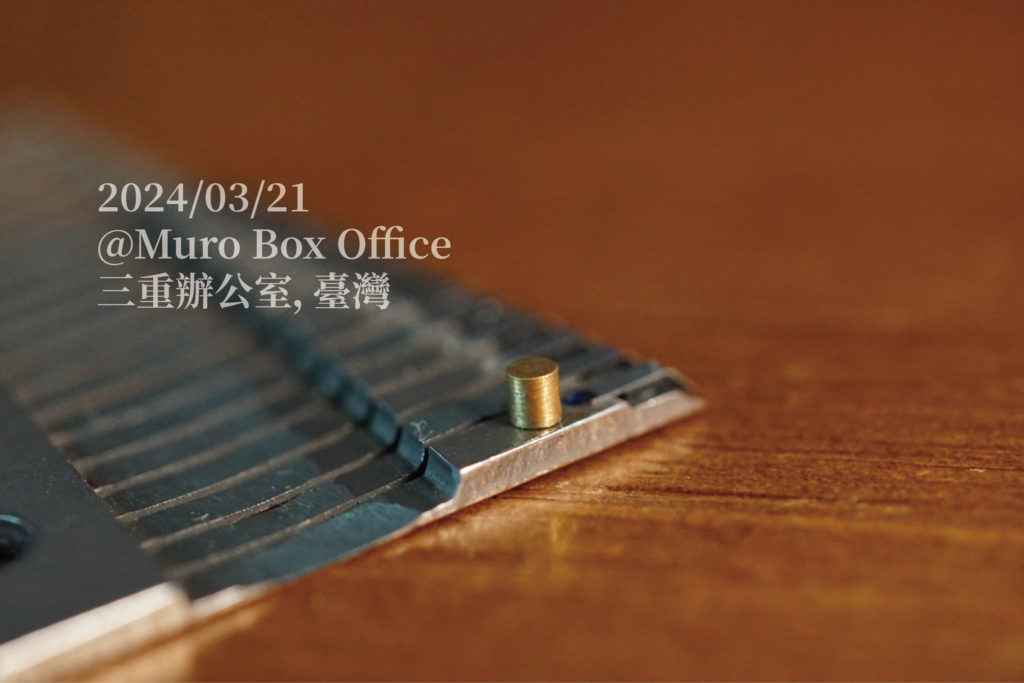
There are two issues with this method of making the tuning weights:
(1)Why brass is used.
(2)How the weights are secured onto the comb teeth.
The reason for using brass is because we aim to utilize a lead-free process, which rules out the use of conventional lead blocks. Brass, being a material with a higher density, is the most common alternative and is readily available with stable processing properties.
However, not using lead affects the method of fixation. Traditionally, lead weights are attached to the comb either by using epoxy adhesive or by soldering.
We cannot accept the use of adhesive as it is a temporary fix rather than a stable production method.
Furthermore, traditional soldering cannot be employed. This is because the comb undergoes heat treatment to enhance its hardness. Excessive heating could lead to annealing, softening the material and affecting the sound. The reason why lead weights could be traditionally soldered is due to the low melting point of lead (327 degrees Celsius), which is below the annealing temperature of the comb’s carbon steel (400 degrees Celsius).
Thus, as long as temperature control is stable, soldering semi-melted lead blocks can be done without annealing the comb. However, brass has a melting point of over 900 degrees Celsius, making it impossible to melt brass blocks at temperatures lower than those causing annealing. Using only standard tin solder to fix brass is insufficient; the connection point cannot withstand repeated vibrations and will loosen.
New Design for Brass Tuning Weights in Muro Box
We have proposed a new method of securing the brass blocks using a mortise and tenon joint. This involves drilling holes at the front end of the comb teeth, allowing the brass blocks to be inserted and wedged directly onto the teeth.
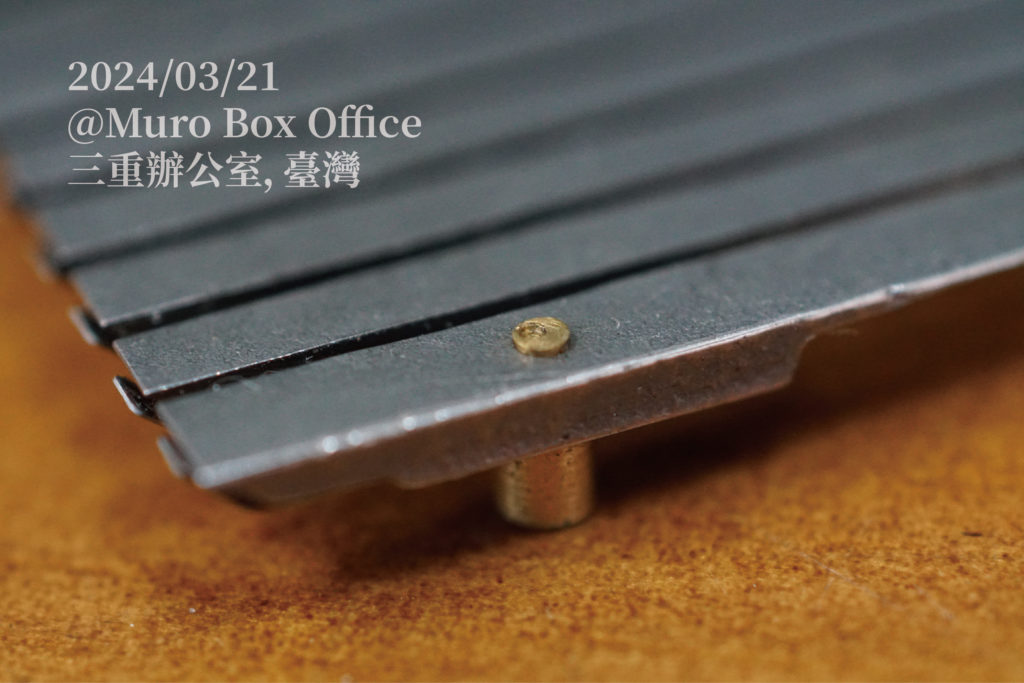
The Difficulty with the New Tuning Weight Design
However, things didn’t end as simply as we hoped. Due to the comb undergoing heat treatment for hardening, conventional drill bits are not hard enough to drill holes in the comb. Unfortunately, due to limitations in raw material procurement, we were unable to drill holes in the comb during the pre-heat treatment stage. So, the step that took us the longest time was finding a way to drill holes in the existing post-production combs.
Ultimately, we decided to use a method not found in traditional music box manufacturing: Electrical Discharge Machining (EDM). In simple terms, this method involves using high-voltage electrical currents to locally vaporize and evaporate the metal on the comb, much like lightning strikes, without overheating and annealing the entire comb.
In order to ensure stable mass production, we even purchased dedicated EDM machines to ensure that the drilling specifications meet our standards. However, this meant waiting for the machines to arrive, causing delays. Additionally, this new process required coordination with the tuning process, which was a first-time attempt for our team. It required extensive communication and coordination to find a stable production method. Therefore, we had to proceed cautiously at the beginning to find a way to produce it steadily.
Shipping Plan
We anticipate that the next N40 update will document the first batch of actual shipments. However, due to the aforementioned reasons, the initial shipping pace will be slowed down. We ask for your patience to ensure that any production issues are not hastily overlooked.
Furthermore, we will initially ship several batches to customers in Taiwan in April. This decision is made because we need to test whether the new shipping packaging can withstand the accident falling by the delivery agent. We will then gradually expand to international shipments.
We appreciate your support. Finally, we are approaching the moment of the first shipment. Just like all of you, I am filled with excitement and gratitude. Thank you for your continuous support along the way.
Muro Box Inventor- Dr. Chen-Hsiang Feng
2024/03/21
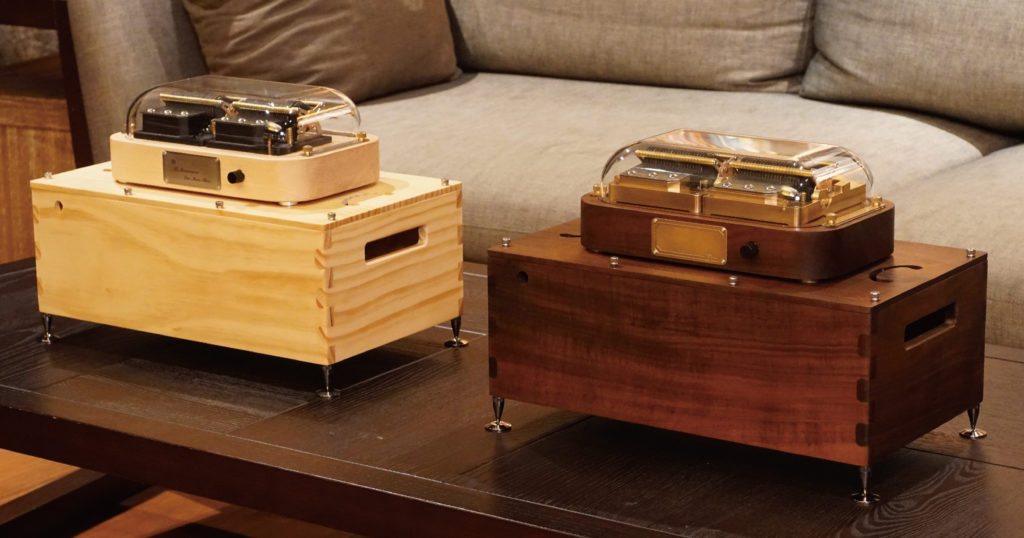