The base is one of the three most important elements of a music box (the comb, the base, and the wooden box), yet it is often overlooked and its significance underestimated. In this article, we will share our experience designing the Muro Box to explain how a well-crafted music box base is designed.
The Key Factor of Sound Quality - The Metal Base
The Transmission of Vibrations Defines the Sound Characteristics
The function of the metal base in Muro Box is to conduct the vibration from the comb to the wooden box. It is similar to the “bridge” of guitar and violin, which conducts the vibration of strings to the hollow wooden boy to create beautiful sound.The “conduction” is the key factor that determines the sound quality, therefore, the material, size, shape, and thickness of the metal base went through a series of experiments.
Next, we will discuss how these characteristics affect the sound.
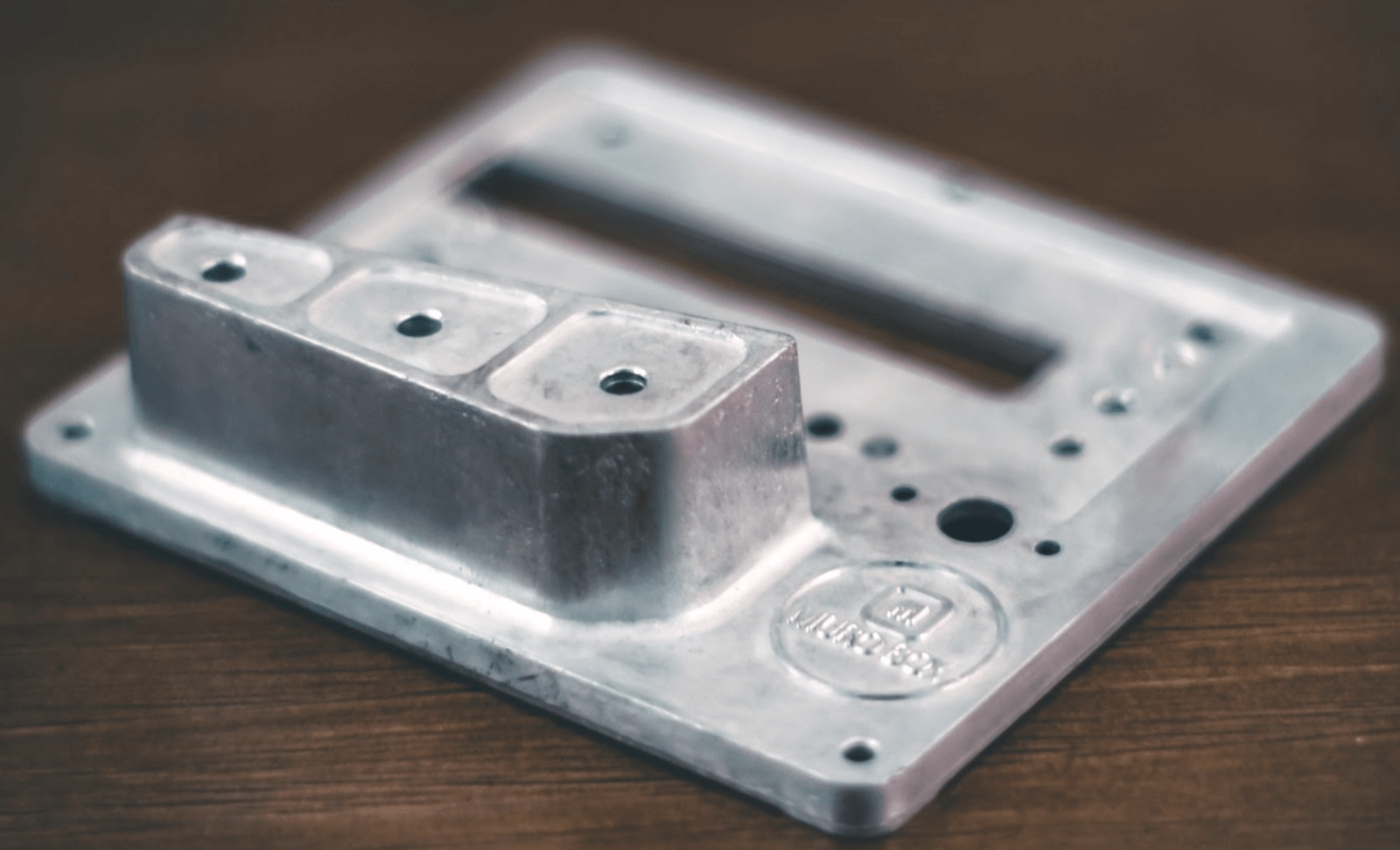
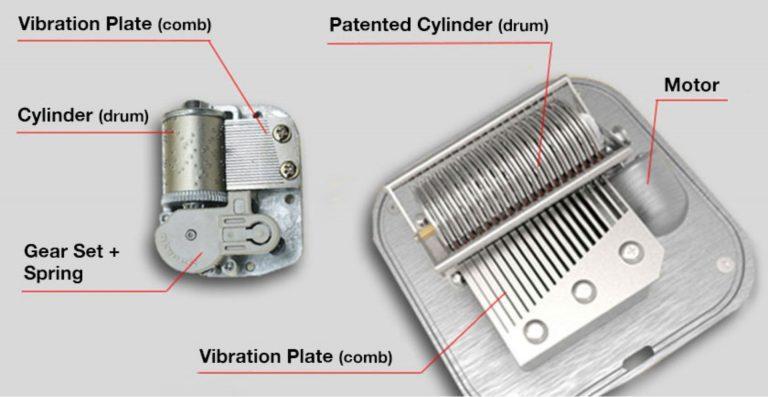
Does a Music Box Base Need to Be Metal?
Have you ever wondered why even the cheapest music box movements always use a metal base? Wouldn’t plastic be more cost-effective? What about 3D-printed plastic? Or 3D-printed metal? Is any kind of metal acceptable?
These seemingly simple questions are actually quite difficult to answer. If the goal is just to produce sound from the music box, then any material would work. However, if the goal is to make the music box sound pleasing—with that beautiful lingering resonance we all love—then the options become much more limited.
The Relationship Between “Lingering Resonance” and the Weight of the Base
When we refer to “lingering resonance,” we specifically mean the duration of the comb’s continued vibration after being struck. Generally, we prefer a longer lingering resonance, meaning the sound persists for a longer time. This is often described as having better “resonance” in the music box.
One key factor affecting lingering resonance is the overall mass of the music box. Modern music boxes, due to their reduced size and often housed in plastic cases, tend to have lower overall mass. As a result, the impression people have of smaller music boxes, compared to classic larger ones, is that they are louder but have shorter lingering resonance. The sound tends to be abrupt and stops quickly, with less noticeable prolongation of the notes.
To explain this phenomenon, we can use the analogy of a reservoir releasing floodwater to illustrate the relationship between mass and sound.
A base with higher mass is like a larger reservoir: it can hold more water, or in this case, more of the vibration energy from the comb, and then release it slowly, resulting in a longer lingering resonance. On the other hand, a base with lower mass is like a smaller reservoir. When the vibration amplitude of the comb is high, or when there’s more energy, the smaller reservoir can quickly become overwhelmed and overflow. This manifests in the sound as excessive volume and what we refer to as “cracked” or broken noise. Additionally, a smaller reservoir empties faster, which means a shorter lingering resonance.
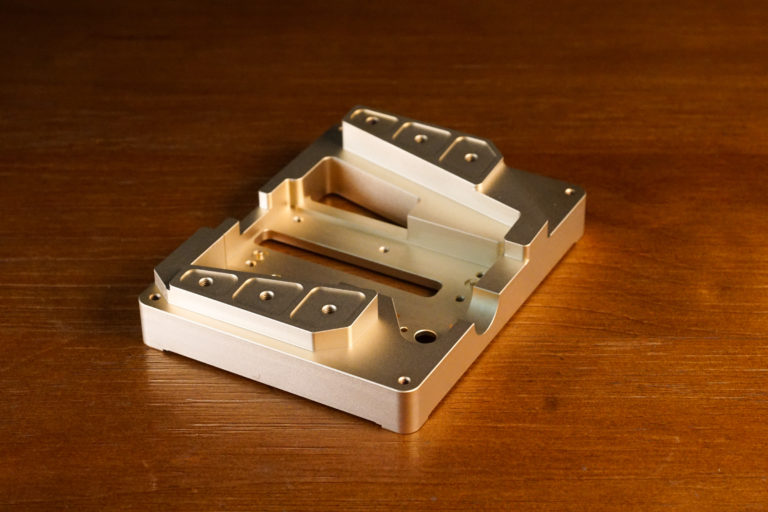
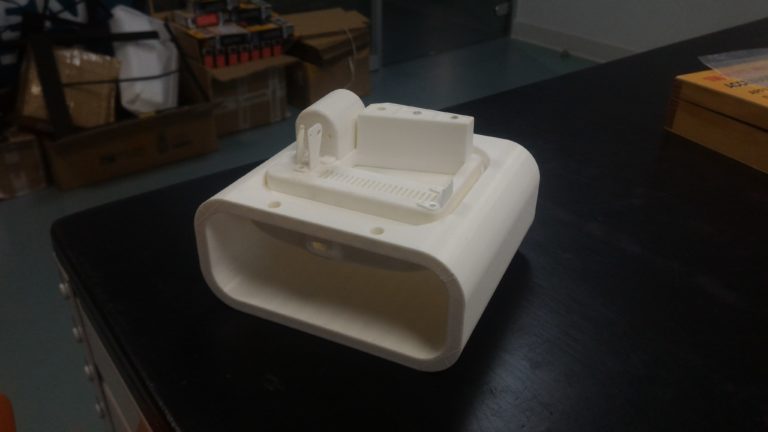
Lingering Resonance and Base Material Choice
Based on our understanding of lingering resonance, we can now evaluate the material for the base.
To extend the lingering resonance, it is essential to increase the mass, so plastic is not suitable, as it will result in a short and fragmented sound. This issue is independent of the manufacturing method, meaning neither plastic injection molding nor 3D printing can achieve the desired result.
During the initial development phase of the Muro Box, we used 3D printing for prototype production. After seeing our prototypes, General Manager Huang shared the following story with us.
In the past, the Institute of Materials Chemistry at the Industrial Technology Research Institute approached Kyooh to replace metal with new polymer materials for the base. Despite the General Manager’s advice against it, they proceeded with development. Unfortunately, the result was poor resonance and doubled production costs, leading to the project’s discontinuation.
While plastic lacks sufficient weight, not all metals are suitable either. For example, aluminum is still too light (about 2.7 g/cm³). General Manager Huang also shared that they had tried using cast iron for the base, but it failed in the end. Although it was heavy enough, cast iron’s hardness produced undesirable sound characteristics. Thus, hardness is also a consideration—it’s not simply a matter of the heavier, the better.
This makes the use of brass in classical music boxes very clear: 1. Brass has a high specific gravity, making it one of the denser metals readily available (about 8.5 g/cm³). 2. Its hardness is moderate, providing a comfortable sound quality. However, its disadvantages are also clear: it is too expensive.
The cost of brass, both in terms of material and processing, is high, and it also rusts easily, which is why brass music boxes are now rarely seen.
Additionally, while metal 3D printing can be used to produce music box bases, its cost is prohibitively high for mass production. Practically, CNC milling is more effective, which is the method used for the brass base of the N40 Sublime.
History of Zinc Alloy
Over a decade of revolution, the material used for the metal base of a music box has gone through continuous modifications. In recent years, there have been continuous attempts with various materials, including copper, aluminum, cast iron, and other macromolecule materials, have been tested.
Nevertheless, no matter how many attempts were made, none matched the comprehensive performance of zinc alloy. The selection of zinc alloy today is the result of extensive testing by predecessors.
Zinc alloy was the best result from huge amounts of tests and trials. Another crucial advantage of zinc alloy was the ease to produce with molds , therefore it is also widely used in products such as faucets, locks, door knobs, car badges, and wine openers. Despite the fact that the price of zinc alloy has increased significantly in recent years, most music box manufacturers still insist on using it.
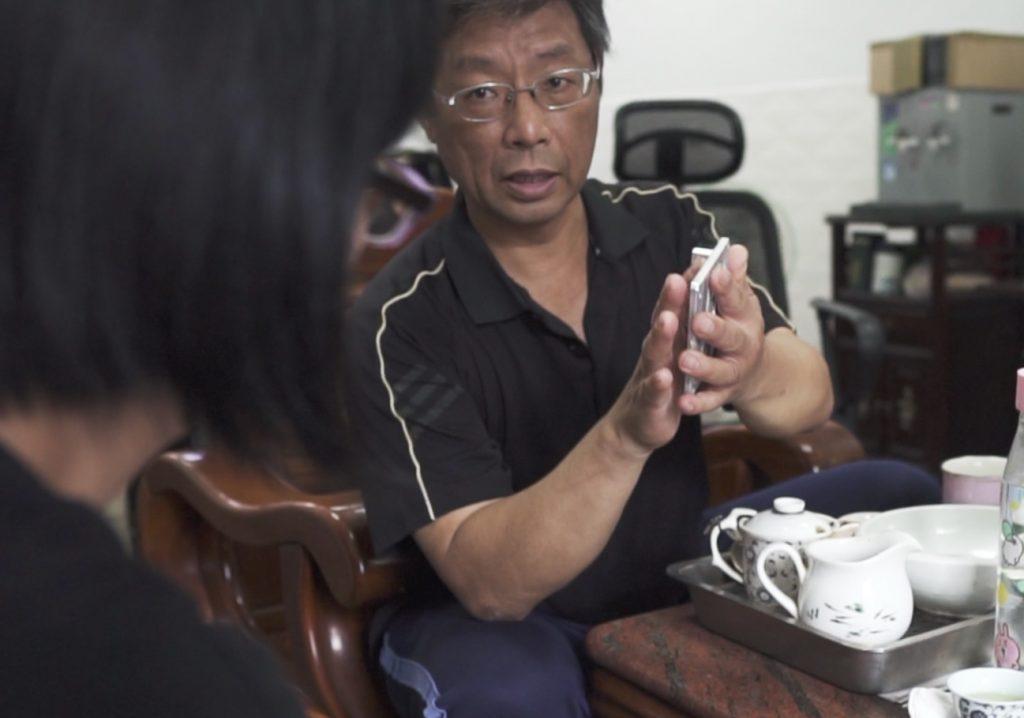
Interview with a Mold Maker
The black base material for the Muro Box N20 and N40 Standard is zinc alloy. To ensure quality, we collaborated with a zinc alloy processing factory in Changhua, which has been in operation for over 30 years and has worked with Kyooh for more than 25 years.
We interviewed Mr. Guo, the mold maker for the Muro Box zinc alloy base, to understand that the molds are crafted close to the precision limits of zinc alloy processing. To achieve this, a modular design approach is used: initial templates are made with copper molds, which are then assembled to ensure precise dimensions before final mold production. Each mold can produce at least 500,000 bases.
Let's Watch How the Metal Based Was Produced!
First, the zinc alloy chunk is placed into a 435ºC metal furnace to melt it. Then it is compressed with a die casting machine with the carefully designed mold to form the precise shape.
After waiting for the cooling, remove the excess material scraps from the parts one by one and return them to the furnace. Then, carefully grind off the burrs with sandpaper by hand. Once the part dimensions are confirmed, wash the parts to prevent grease and other contaminants from causing the paint to peel off. A sticker designed by Kyooh Precision Industry Co. Ltd. is affixed to the top of the base to ensure direct contact between the comb and the base, preventing the paint material from affecting the transmission of sound to the zinc alloy base, ensuring a bright tone.
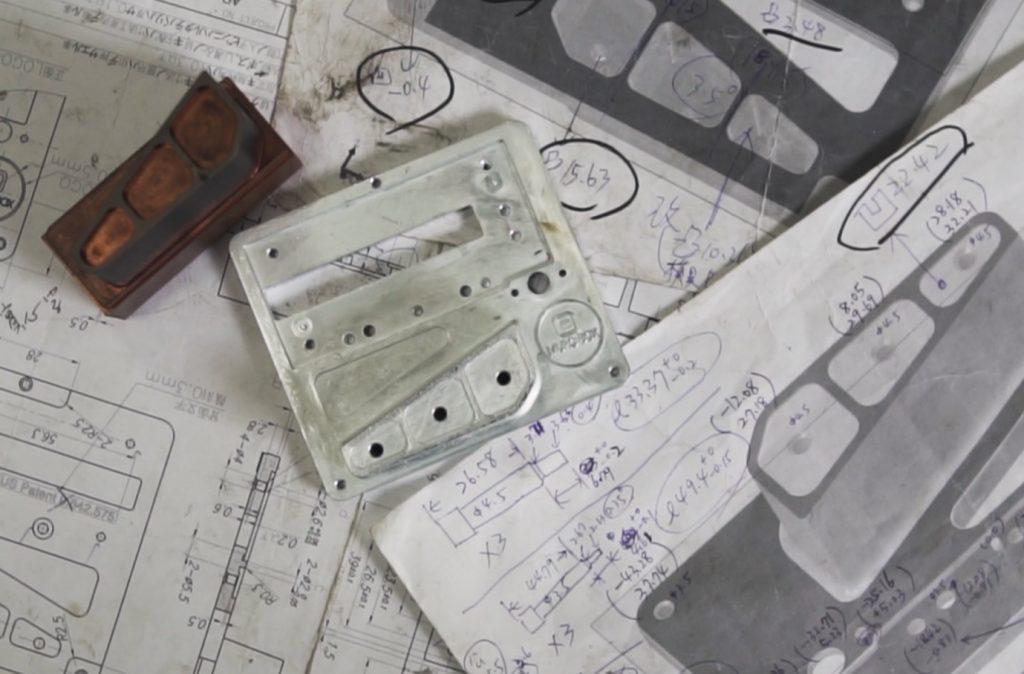
The Design of the Metal Base
The design of the metal base is based on a traditional music box. Our design principle is “less is more”, and each part has its own practical function.
Here, I would like to share some less-known key aspects of base design.
Why Does the Base Have Holes and Indentations?
Have you ever closely observed the design of a music box movement and wondered why there are indentations and openings? Is this design intended to improve sound quality?
In reality, the opposite is true. These design features are primarily used to reduce costs. The thinner the base, the less metal is used, which lowers production expenses.
However, if the base is too thin, it results in insufficient weight, which negatively impacts the lingering resonance. The real challenge is to reduce the amount of metal while still maintaining the same level of sound quality. This is a key strength of Kyooh in Taichung and highlights the fundamental difference between Taiwanese and Chinese-manufactured music boxes.
As for the Muro Box bases, given the different pricing, we do not need to cut costs here. Whether it’s the zinc alloy base or the brass base, the entire base is solid and does not require openings or indentations.
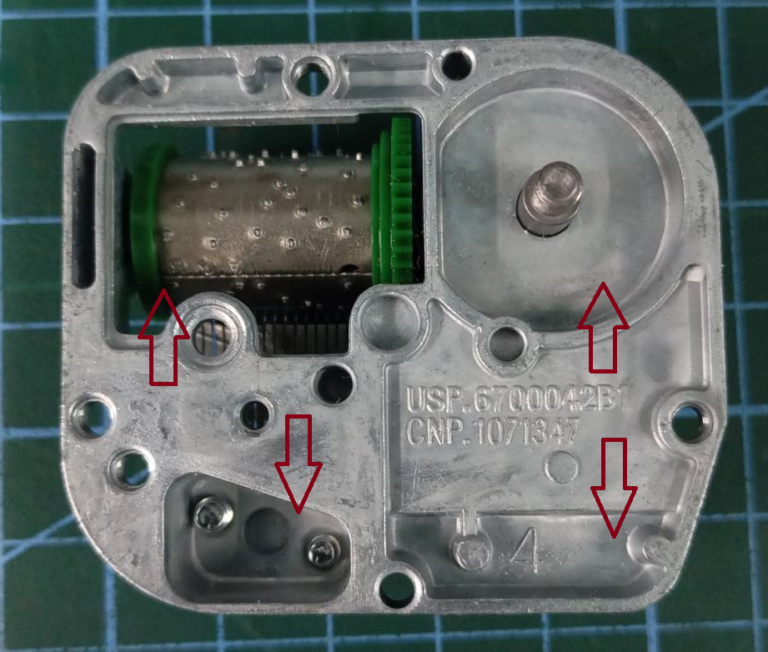
Does a Heavier Base Mean Better Performance?
Earlier, we mentioned the concept of the base acting like a reservoir. Some may wonder, wouldn’t an infinitely heavy base be even better? The answer is no, it wouldn’t be. If the force of the comb’s vibrations is insufficient to drive the entire music box, the result would be a very soft sound.
The volume of the sound corresponds to the amplitude of the sound waves. If the base is too heavy, it may cause the music box’s vibrations to be too small, which in turn makes the amplitude of the sound waves too small, resulting in a quieter sound. For example, if the N40 Sublime’s brass base weren’t equipped with a double comb, its sound would actually be weaker compared to the standard N40 model. In fact, the N20 is the loudest among all our models.
This is also why high-end music boxes tend to sound quieter. They typically have heavier bases, which suppress the volume. In contrast, smaller music boxes often sound louder, but since their vibrations are larger, they consume energy more quickly, leading to a shorter resonance.
Therefore, the weight of a music box’s base must be matched with the vibration plate being used—it’s not simply a case of heavier being better. This is also one of the important reasons for adding a damper to the comb.
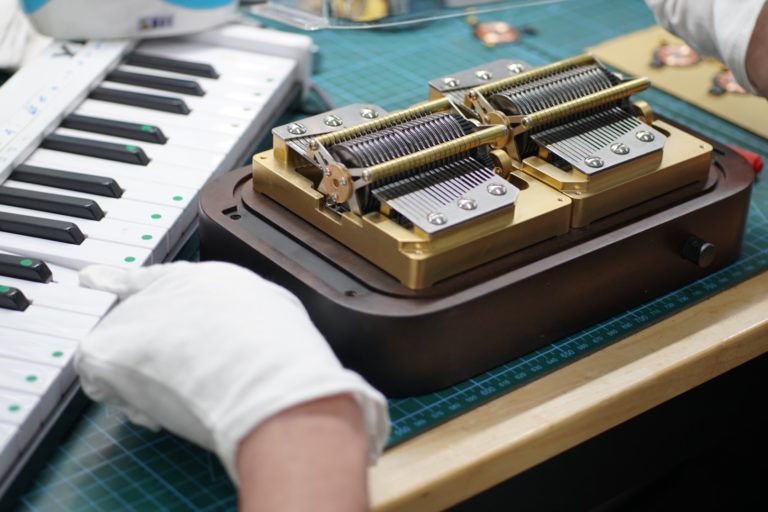
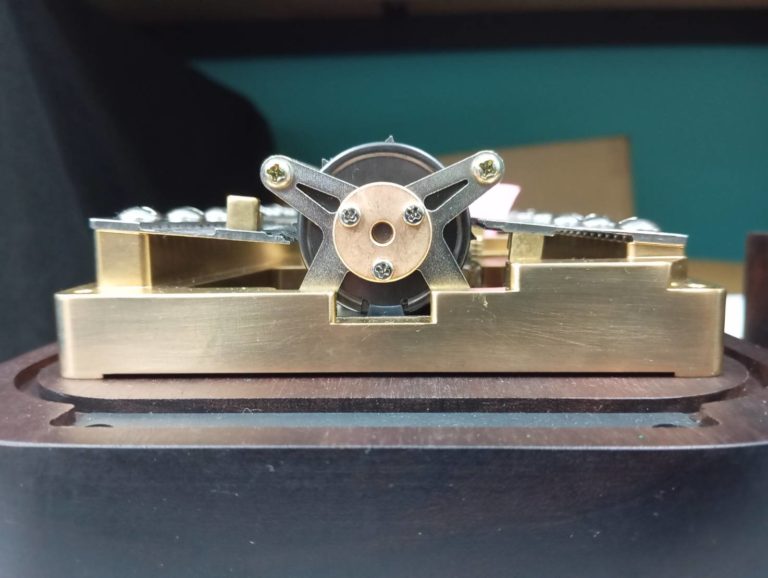
The Positioning of the Comb
Have you ever wondered how the comb of a music box interacts with the cylinder? Intuitively, one might think the comb is positioned vertically and placed in the middle of the cylinder, right? However, the optimal position for the comb is not quite like that.
In the design of the N40 Sublime, the angle between the comb and the cylinder is 85 degrees. Initially, we did not know the reason for this angle and simply aimed to mimic the design angle of Swiss music boxes. However, after completing the Sublime design, I clearly understand the advantages and disadvantages of this angle.
The primary reason for this design is to enhance the damper’s performance. This angle increases the contact time between the cylinder’s pins and the damper, thereby improving the damper’s shock absorption capabilities.
Additionally, this angle makes it easier to assemble the comb. With the same spacing, the comb with an angle is lifted less by the cylinder’s pins, making it easier to balance the volume of high and low notes during assembly.
However, this design also has its drawbacks. Since the screw holes for the comb are not perpendicular to the base, it poses significant production challenges. For mass production, this design angle would likely be the first to be abandoned.
How Does the Shape of the Base Affect the Sound?
From my observation, the shape of the base does affect the sound, but it’s not very intuitive. For example, the image shows an engineering sample of a base during Muro Box’s development. The arrow points to the openings in the zinc alloy. The triangular hole mimics the openings found in traditional music boxes. At the time, we didn’t understand the principles of sound, so the opening was purely for decoration. The rectangular hole, on the other hand, was reserved for the control signal wires of the cylinder.
The issue with this design is that if the sound waves travel along the perimeter of the opening in the zinc alloy, and the path happens to be an integer multiple of half the wavelength (λ), the sound waves will cancel each other out. As a result, it may sound like certain notes are “missing.” This is a common issue encountered in instrument design that needs to be avoided.
After noticing this problem, we decided to remove the triangular opening in the final zinc alloy base design. Unfortunately, the opening for the cylinder’s signal wires is necessary and cannot be eliminated. However, with the thicker copper base, the sound path inside becomes more complex, so there’s no need to avoid this opening anymore.
Conclusion: The brass base of the N40 Sublime version retains this triangular opening to allow space for the brass weight’s vibration. In contrast, the triangular opening has been removed from the zinc alloy bases of both the N20 and N40 standard versions to avoid impacting sound transmission.
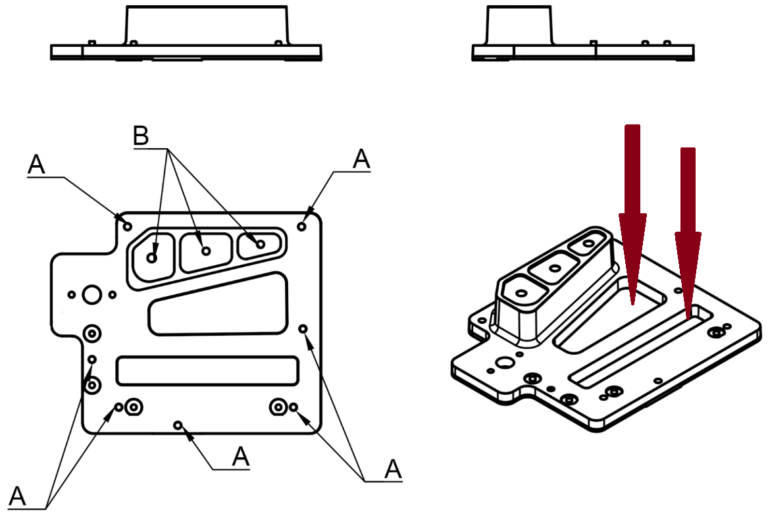
Conclusion
Due to the high development costs of the metal base, once confirmed, design changes will not be made easily. Hence, there are actually very few people in the world who have truly designed music box bases, and related design documents are extremely scarce. Here, we would like to share the issues we encountered while designing the Muro Box base, so that future designers can create better designs more quickly. This can be considered a small contribution to the music box community.