Development History of Muro Box-N40
Hello everyone,
I’m Dr. Chen-Hsiang Feng, the inventor of Muro Box.
During the development journey of the N40 from 2022 to 2024, we once again faced a series of critical decisions and no shortage of tough engineering challenges.
In 2016, we decided to start a business together as a couple. We visited music box shops and factories before ultimately deciding to develop an app-controlled and programmable music box. If you’re interested in learning about the key moments that led us to this entrepreneurial decision, feel free to read this story: Why We Invented “Muro Box”?
(Last updated: July 7, 2025)
The Crossroads of the Company's Future Directions
In early 2022, we realized that our existing customers/subscribers started to feel tired of reading about the news of the existing N20 models (Standard and Lite). They continually expressed a desire for a new model. At that time, we had two potential directions: one was to create a higher-end model, the N40, while the other was to move in a more affordable direction, which we called the N20 Lite SE. This would be similar to the iPhone SE concept, using downgraded specifications to offer a lower price for boosting its sales, with costs recovered through app service fees.
Considering our limited human resources, we could only choose one product line to develop at one time. Since the customer bases for both models were completely different, the choice of the next product line essentially determined the future direction of the company. Therefore, the true decision behind it all was how we wanted to shape the Muro Box brand.
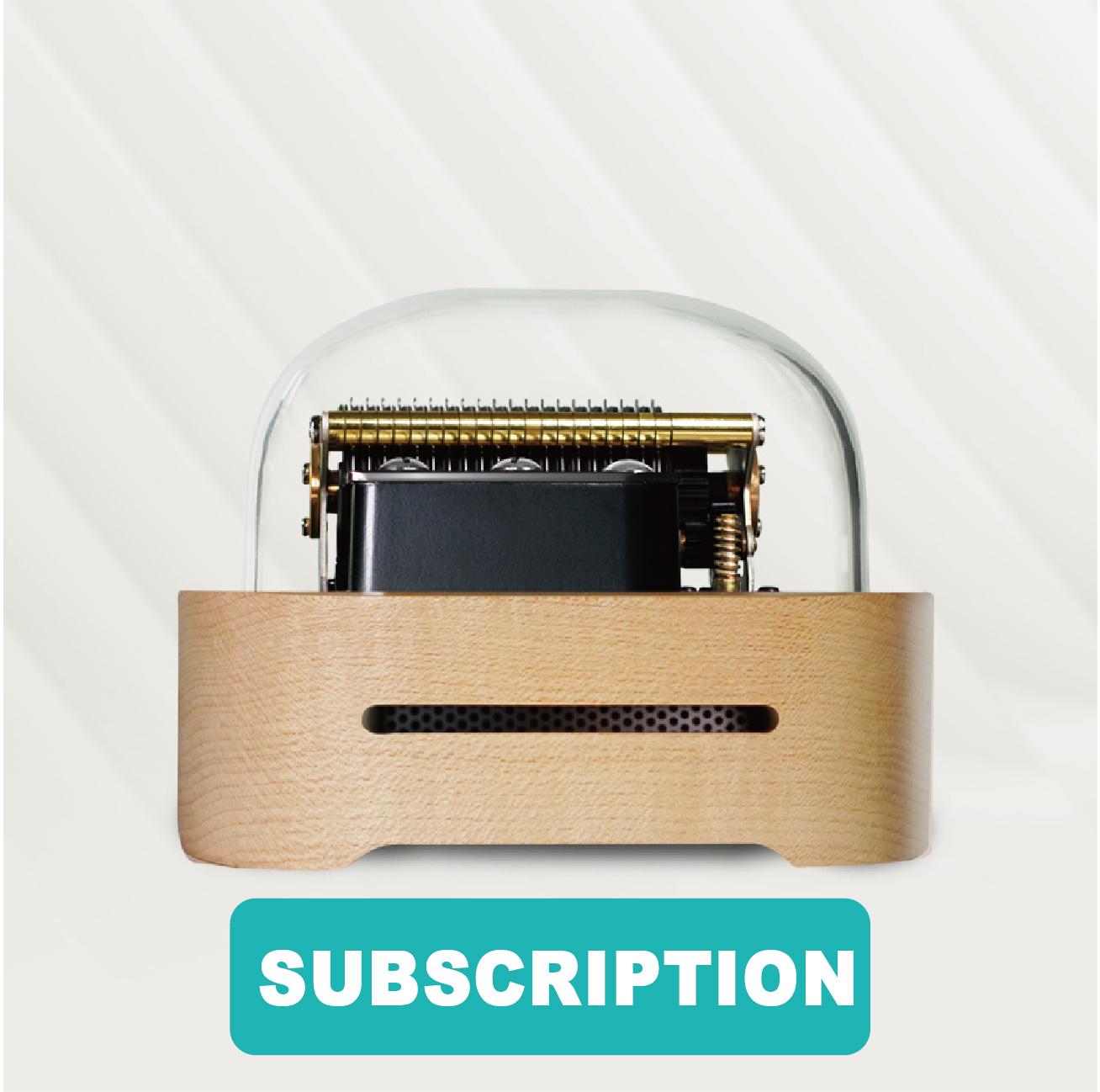
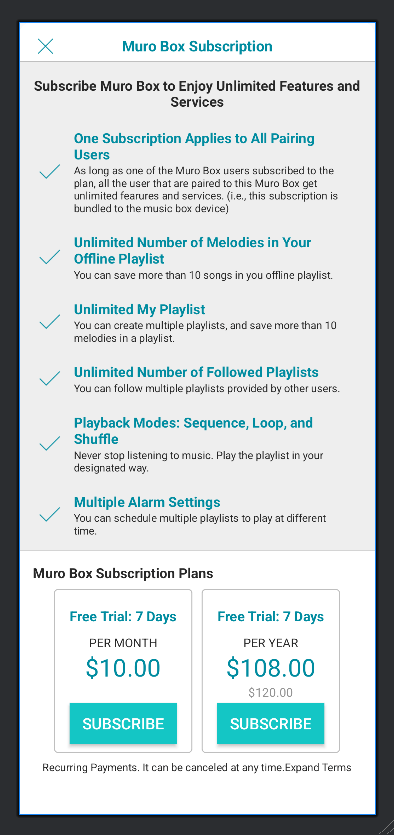
The N20 Lite SE: Our Former Choice for a More Affordable Model
Everyone can probably understand that the customers of the high-end N40 model, whether using the music box as a collectible or as an instrument, are certainly not accustomed to using an app. Therefore, the key focus of developing the N40 was on mechanical design, not the app. On the other hand, since the N20 Lite SE uses a software-based payment model to lower the hardware price of the music box, the key focus of its development was adding app features.
At that time, we had a dedicated backend engineer, an app engineer, and a firmware engineer (myself), and we even hired a software intern. So now, the situation was a bit awkward—if software development wasn’t the main focus, how could I find enough tasks for them to do?
But back then, I was still unfortunately making decisions with an engineer’s mindset: to match the current team structure, the next product should be the low-cost N20 Lite SE.
Additionally, the lower price aligned with general consumer expectations, so we thought an increase in sales would be anticipated. After all, we had never sold a more expensive music box. How could we promote a music box that would cost more than 1000 USD? Just the thought of it sent shivers down my spine.
Lowering Prices Can Boost Sales: A Problematic Hypothesis
As the software development went on at full speed, I felt a stronger sense of uncertainty. I can hear an inner voice warning me that N20 Lite SE would fail. I assumed that a lower price would lead to higher sales, but that wasn’t necessarily true.
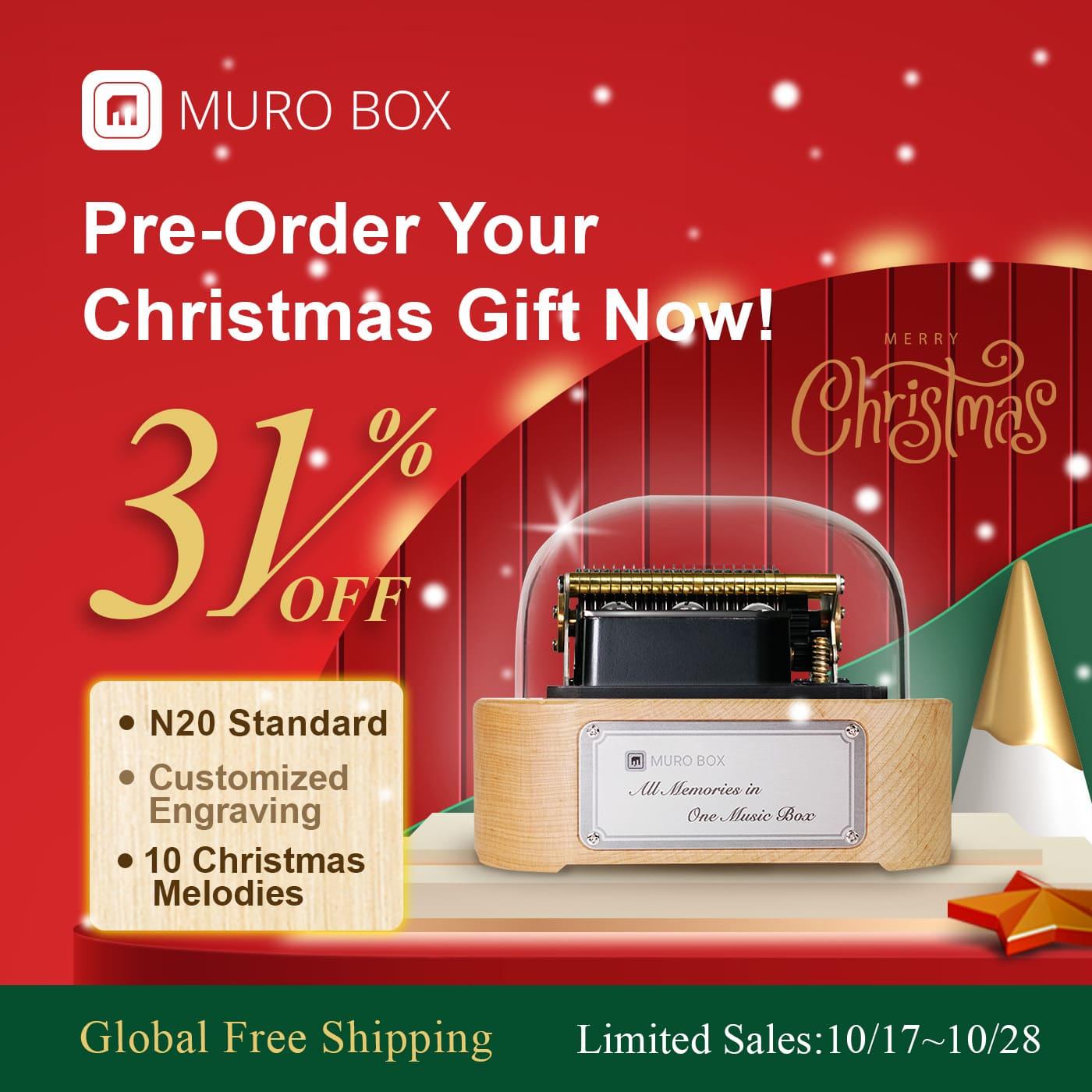
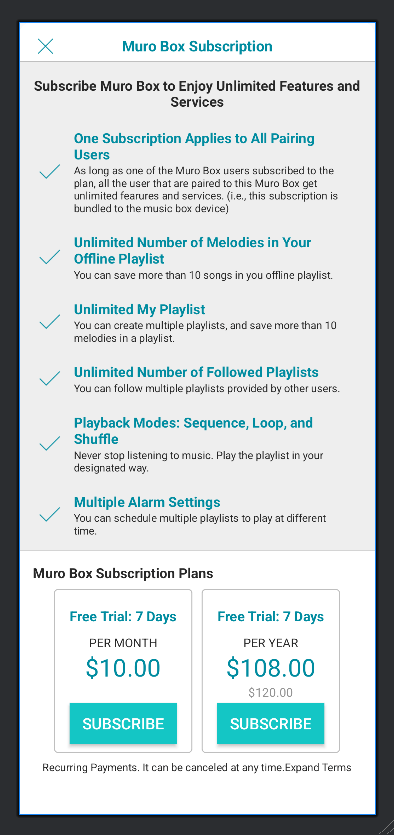
Subsidizing Hardware with Software Subscription Fee Cannot Support Our Actual Cost
Even if lowering the price leads to an increase in overall sales, discounts will also reduce actual profits. Moreover, the hardware costs of the music box are fixed, so how much room is there left for discounts?
Our lower price is built on the fact that there will be paid software. Following the common practice of charging under ten USD dollars for the app, how many subscribers are needed just to support the salary of one engineer? Can our company’s resources sustain losses until we reach ten thousand subscribers?
The Final Moment: Reluctantly Remove the App's Paid Model
But by this time, the software development was already nearing completion. The new system had a scheduled launch date, and I found myself caught in a dilemma —should I release this app version despite the fact that it is likely to fail, or should I stop this entire fiasco immediately?
Finally, on the first day of the system launch, I had an epiphany. I pressed the emergency stop button and asked the team to completely remove the N20 Lite SE version just one day after it was launched.
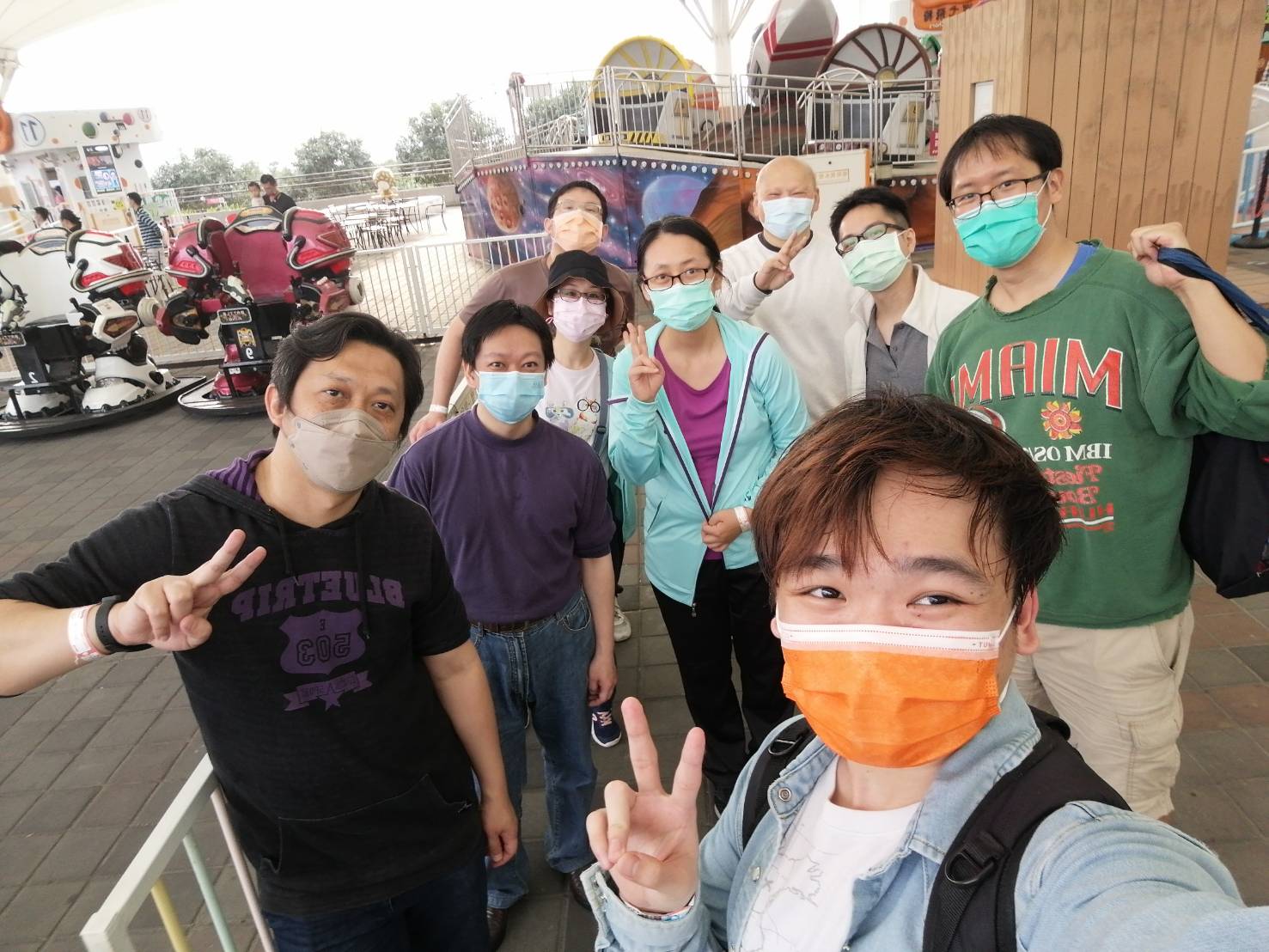
The Consequences of Making a Wrong Decision
Just as I chose the N20 Lite SE for my software team, when I gave up this direction, the software team collapsed instantly. The app engineer lost his confidence in the product and immediately tendered his resignation.Due to the current situation, which is indeed unfavorable for the continued development of the app, I could only advise him, based on our past camaraderie, to stay for one more month to complete the handover before leaving. I had hoped the intern could help share the pressure, but to my surprise, he saw the writing on the wall and informed us via a Line message that he was quitting the project immediately. This was a sudden and irresponsible resignation.
Due to my wrong decision, while wasting everyone’s time, the company was severely impacted. After stabilizing the remaining staff, I had to carefully consider our next step.
The N40 Music Box and N20 Battery Model Became Our Last Hope
My remaining options were the development of the high-end N40 model or the addition of a battery to the N20 model. With limited time and funds, and unable to bear another failure, I decided to pursue both directions simultaneously. I took charge of the high-end N40 development, while outsourcing the battery model of the N20.
Unexpectedly, after announcing the decision to pivot towards developing the N40, not only did multiple customers emailed us for making the right choice, but our distributor in South Korea also expressed his gratitude for our decision. When I explained this decision to the General Manager of Kyooh Precision Industry in Taichung, he also disagreed with my previous N20 Lite SEL model for a more affordable price.
I was stunned. If everyone around me believed we shouldn’t have gone down that path, why didn’t I feel it at the time? As a decision-maker, I failed to heed the many warning signs, and for that, I am truly sorry to every team member and supporter of this project.
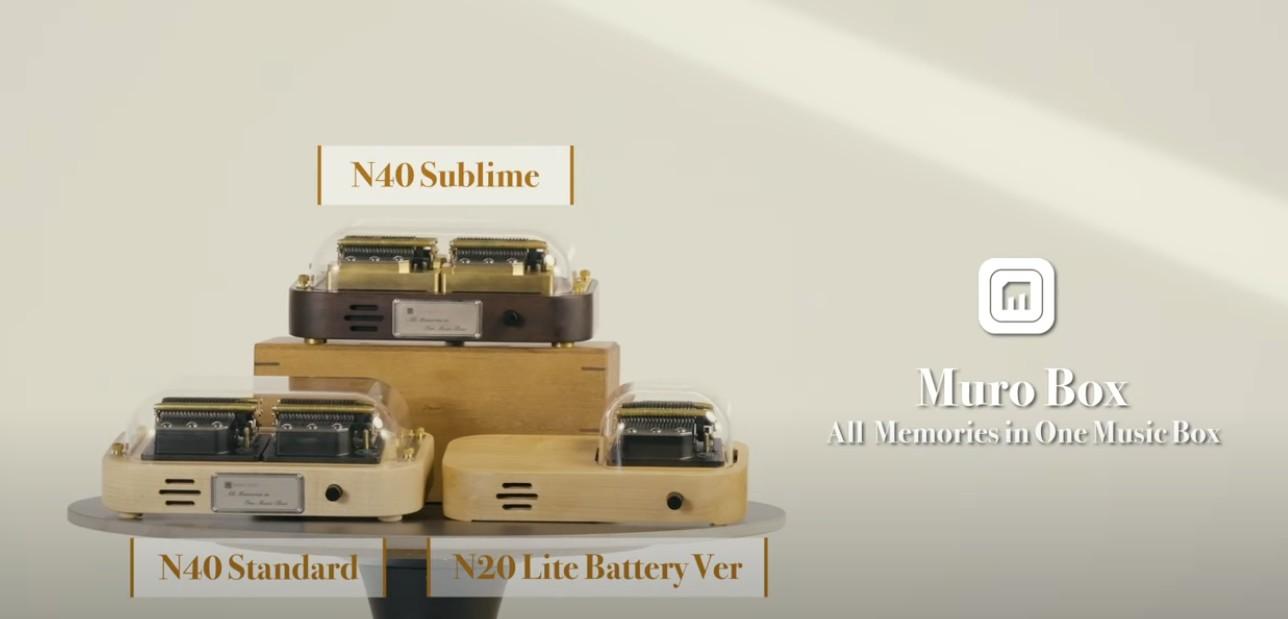
Change Our Direction to Restart
Since the team had just gone through a failed app project, I urgently needed a milestone victory to restore their confidence. At that time, I chose to apply for the CITD (Conventional Industry Technology Development) project subsidy with the product idea, “Muro Box-N40”. Although the application was successfully approved and completed, I personally spent a significant amount of time preparing the paperwork, which, to some extent, delayed the development schedule for N40 music boxes.
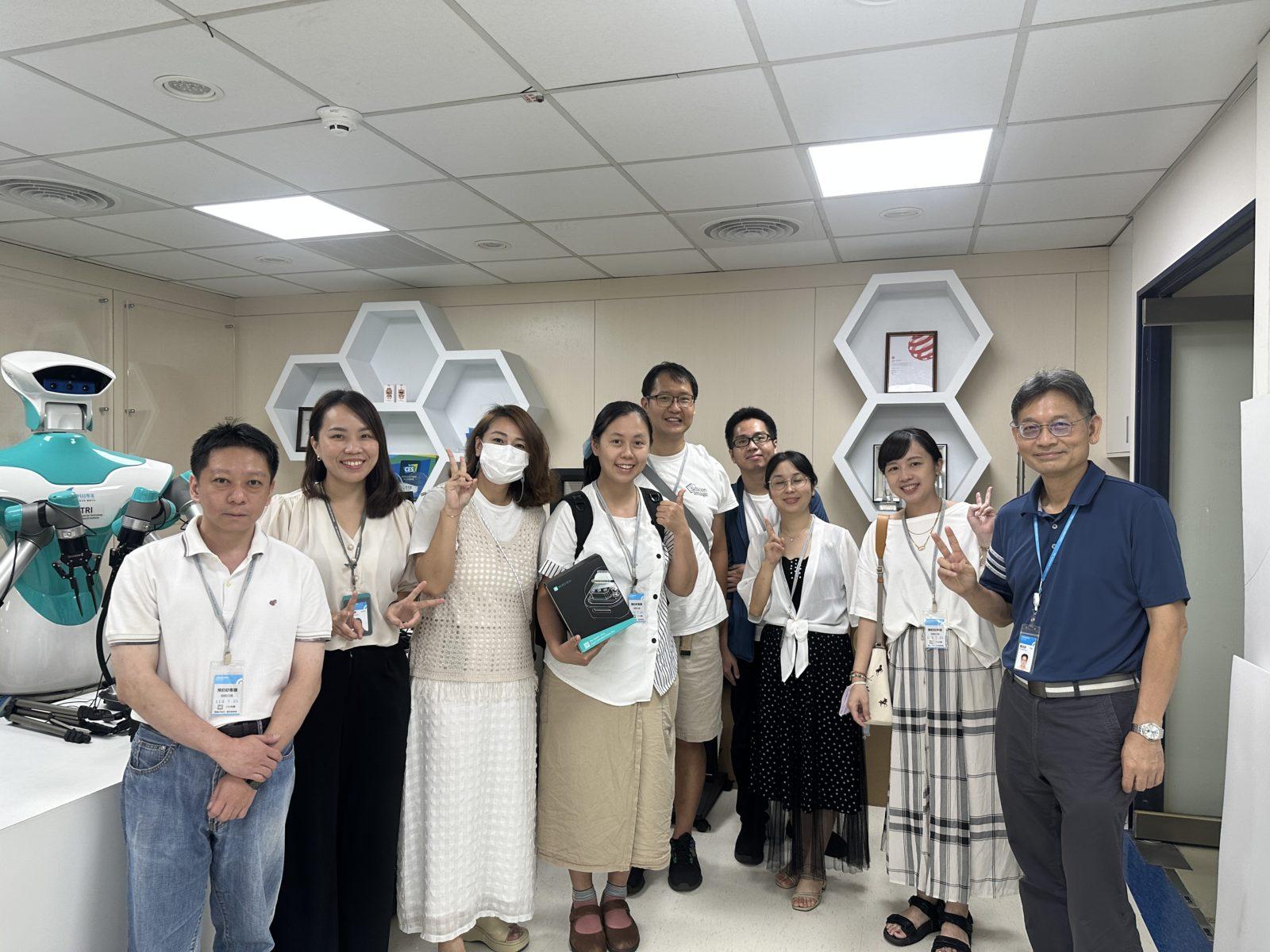
At the same time, ITRI (Industrial Technology Research Institute) provided timely assistance. Since one of the staff from the IoT Integrated Service Center (IisC) has sponsored the first-generation model of Muro Box-N20 on our Zeczec crowdfunding campaign, they have supported us in various ways. This time, I borrowed equipment from IisC and took the entire team to visit their office. I wanted to show the team how important the music box we were working on was and how many people were expecting its success.
However, we could no longer afford to waste any more time. Since then, we finally adjusted our mindset, and the N40 project was launched immediately.
The N40 Project was Officially Started
At this point, the progress of the N40 is like a chaotic mess, with only some scattered experimental parts left on the table and no comprehensive product development plan in place to proceed step by step. Our previous intermittent experimental results show that our handmade sample could connect two N20 units to simulate the operation of the N40. Apart from that, we have practically nothing in hand. It’s like trying to find a needle in a haystack—so many possibilities, but no clear direction to start the experiments.
To determine the direction of the design, I decided to visit the Music Box Museum in Taichung. My goal wasn’t to focus on the most common Japanese Sankyo brand music boxes, but rather to examine the older European and American music boxes in the museum’s collection. Although these European and American brands have long disappeared, I was clear that returning to vintage designs would be the core of this project. What I aimed to do was blend the oldest music box hardware design with the latest technology, as this contrast would be the key to success.
▲ We used two units of a Muro Box-N20 music box to complete the actions of a Muro Box-N40 music box. At the same time, we also tested the feasibility of using two N20 vibration plates.
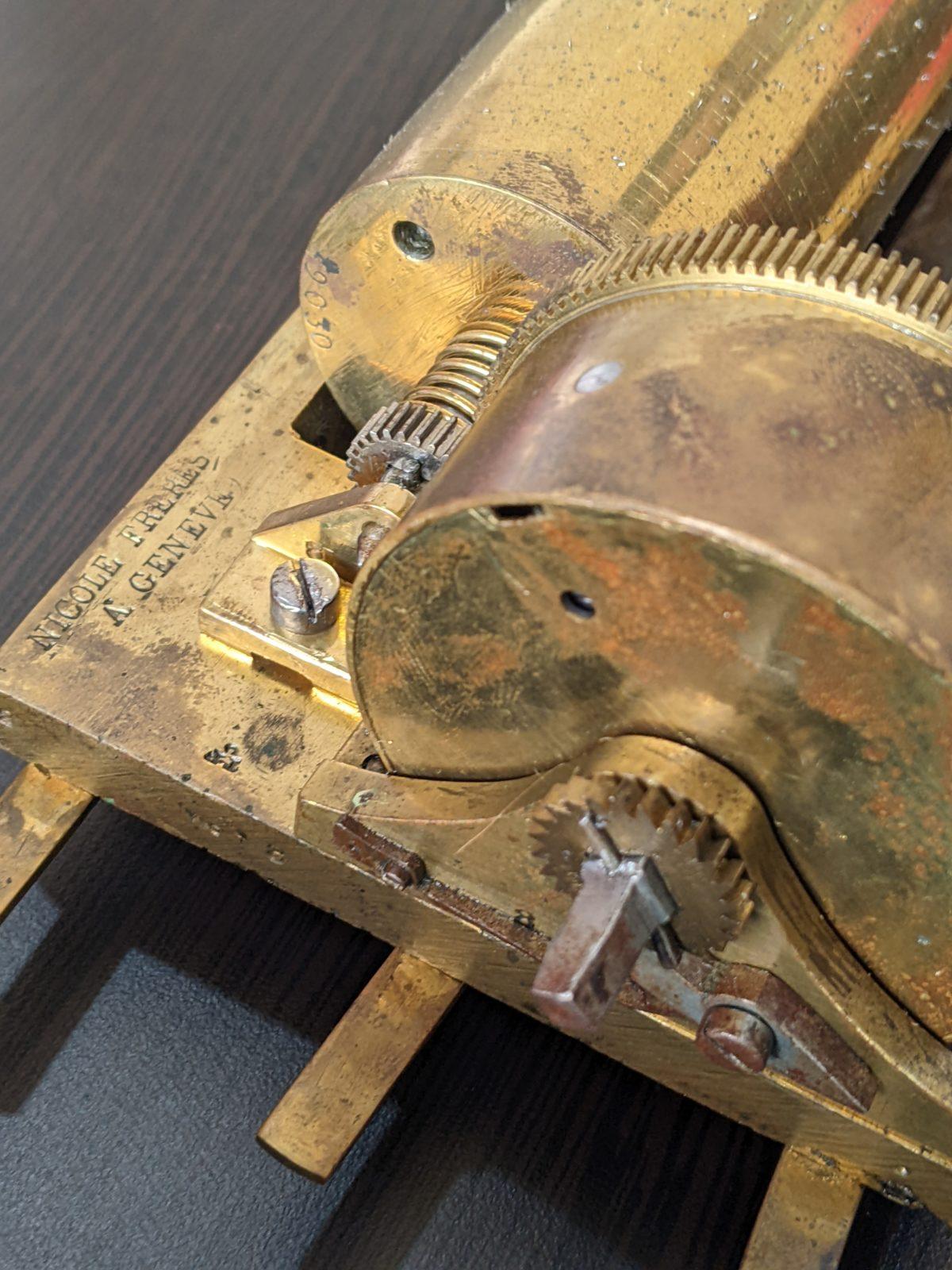
After multiple visits to the Music Box Museum, we discussed with General Manager Huang of Kyooh Precision Industry, which has been producing and exporting traditional music box movements for over 40 years. We concluded the following design directions:
Playing 40 notes with a single vibration plate would be too risky for Kyooh’s comb design and for our product development. Since we were able to combine two N20 units to achieve a 40-note music box, we decided to continue investing in this direction.
The music box’s size should be increased. Whether for better sound or greater presence, the bigger the better.
The base could be made from brass.
With the main components of the music box—base, comb, and wooden box—decided, the real challenge just began.
(If you’re interested in the history and production process/technology of traditional music boxes, feel free to read this story: The Birth Place of Music Box)
The Base
Although the N40 was essentially just combining the bases of two existing N20s, its little change made it look too boring. But no matter how I thought about it, I couldn’t come up with any other variations. While I was daydreaming, I suddenly had an idea: since the points on the cylinder are symmetrical, why not insert multiple combs toward the cylinder like a hedgehog, so that when it turns, several combs can play simultaneously? Wouldn’t that look cool?
Just as I was excited about this idea, a customer’s previous suggestion suddenly came up in my mind. I remembered that he once asked if we could design a music box that can generate the “Sublime Harmony”. Thinking about it, this would require the cylinder to strike two notes at once, meaning we’d need to insert two vibration plates—which happens to be exactly what I was aiming for! Although I did not fully understand how it worked, it seemed like a great idea worth trying!
(Note: The Belgian customer Siegfried, who gave me the suggestion for using Sublime Harmony, later purchased the N40 Sublime version. Welcome to read the story he wrote, which documents the inspiration he provided for our product development and his N40 Sublime user experience.)
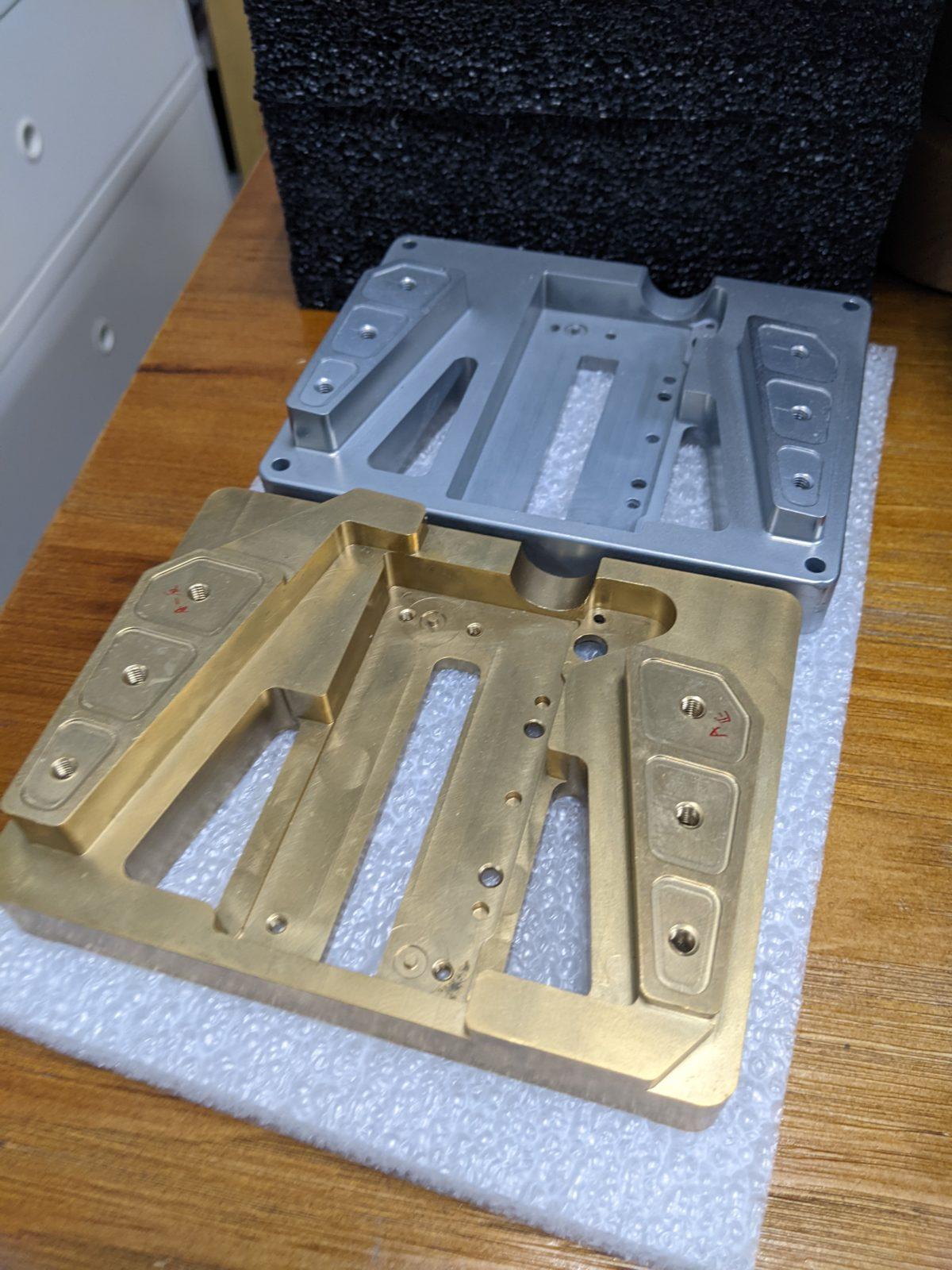
But brass rusts so easily. We left the machines ready for shipment on the table, and the next day, there was a palm print on them. Just touching them makes them rust. What am I supposed to do with this? It was driving me crazy! We bought various anti-rust agents for brass and tested them. During the experiment, I had to squat on a low stool due to the various washing actions, and my colleague joked that I looked like an elderly woman at the market squatting by the roadside washing vegetables. However, after washing and testing, we finally found the proper technique and solved the rusting problem during the assembly phase.
Welcome to read the complete base development process:
Comb
Although we hoped to create a 40-note music box using a single comb, this was ultimately not feasible. At least we tested it with the N20’s vibration plate and found it workable, which should have put my worries to rest. But I was wrong.
To be compatible with the songs for the 30-note paper-strip music box (made in China), which is widely used globally, we had to reduce the originally proposed music scale. Each design change triggers a chain of consequences, and this small adjustment ultimately forces us to modify the vibration plate to the point where it no longer resembles its original form.
After adjusting the music scale, we noticed that the lower notes were too quiet to meet our shipping standards due to insufficient strength after tuning. This isn’t due to any technical shortcomings at Kyooh Precision Industry Co., Ltd., but rather because the original 30-pitch range paper-strip music box had chosen pitches that were too low, resulting in almost no sound in the original model, which is a design flaw. However, this is not a reason for compromise; we must resolve this issue.
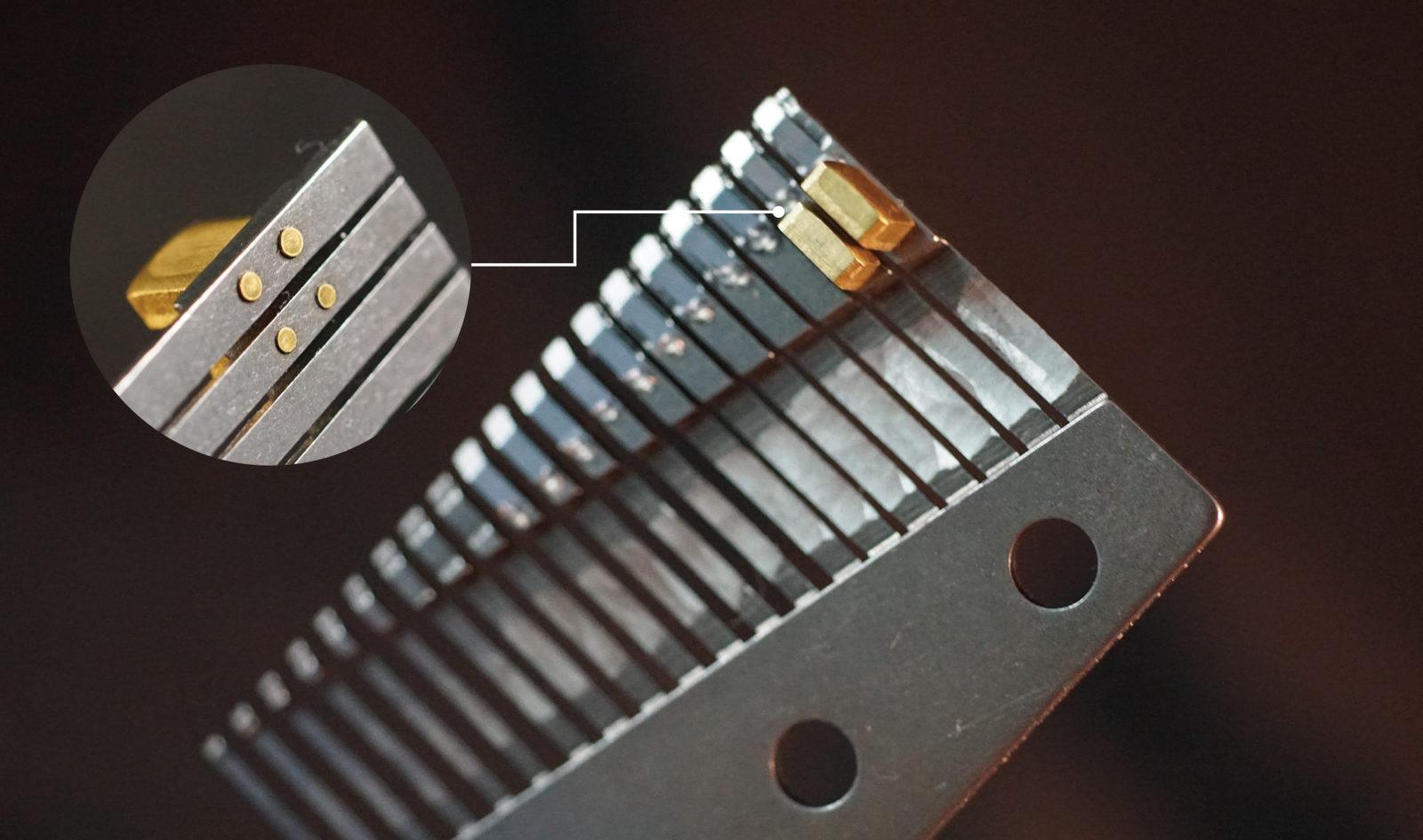
The solution is simple: we need to add a tuning weight beneath the comb to increase the weight. This seems like a normal thing for a music box, but the problem is that Kyooh Precision doesn’t have a production line for installing tuning weights, and they aren’t willing to redevelop their comb for N40. The patent they hold involves removing the tuning weight from the comb in a way that doesn’t affect the sound, whereas my request is to add the tuning weight back, which is completely opposite to their factory’s production guidelines.
But I believe our friends will understand—when we encounter something like this, we always think outside the box in order to conquer the limitation.
So, we purchased a dedicated discharge machining tool, starting with drilling, defining the tuning weight based on the music scale, and reinvented the vibration plate’s weight distribution.
Unfortunately, the butterfly effect struck again. Due to the change in the vibration plate weight, the defect rate of our previously designed damper increased its abnormal rate, causing us to face an endless rework situation with vibration plates due to noise issues. To resolve this, once again, we reinvented the damper for the vibration plate.
Maybe we’ve been too reckless, but through this opportunity, we have gained a deep understanding of many of the vibration plate’s core technologies. We also eliminated the noise that existed in the comb’s damper from our previous designs. This will surely become a solid foundation for the design of our next-generation product, the N60.
The Complete Development Journey of the Comb:
Wood Box
The General Manager of Kyooh Precision Industry Co. Ltd. (Mr. Huang) has repeatedly reminded us that the Muro Box-N20 is too small and making it less attractive when displaying it in the music box museum. However, increasing its size would require changes to the manufacturing process. Therefore, we searched extensively within Taiwan for possible production methods. During this period, we visited a bent wood shaping factory in Changhua, a mass production guitar factory in Yunlin, a glass factory in Miaoli, a violin workshop in Taipei, etc.
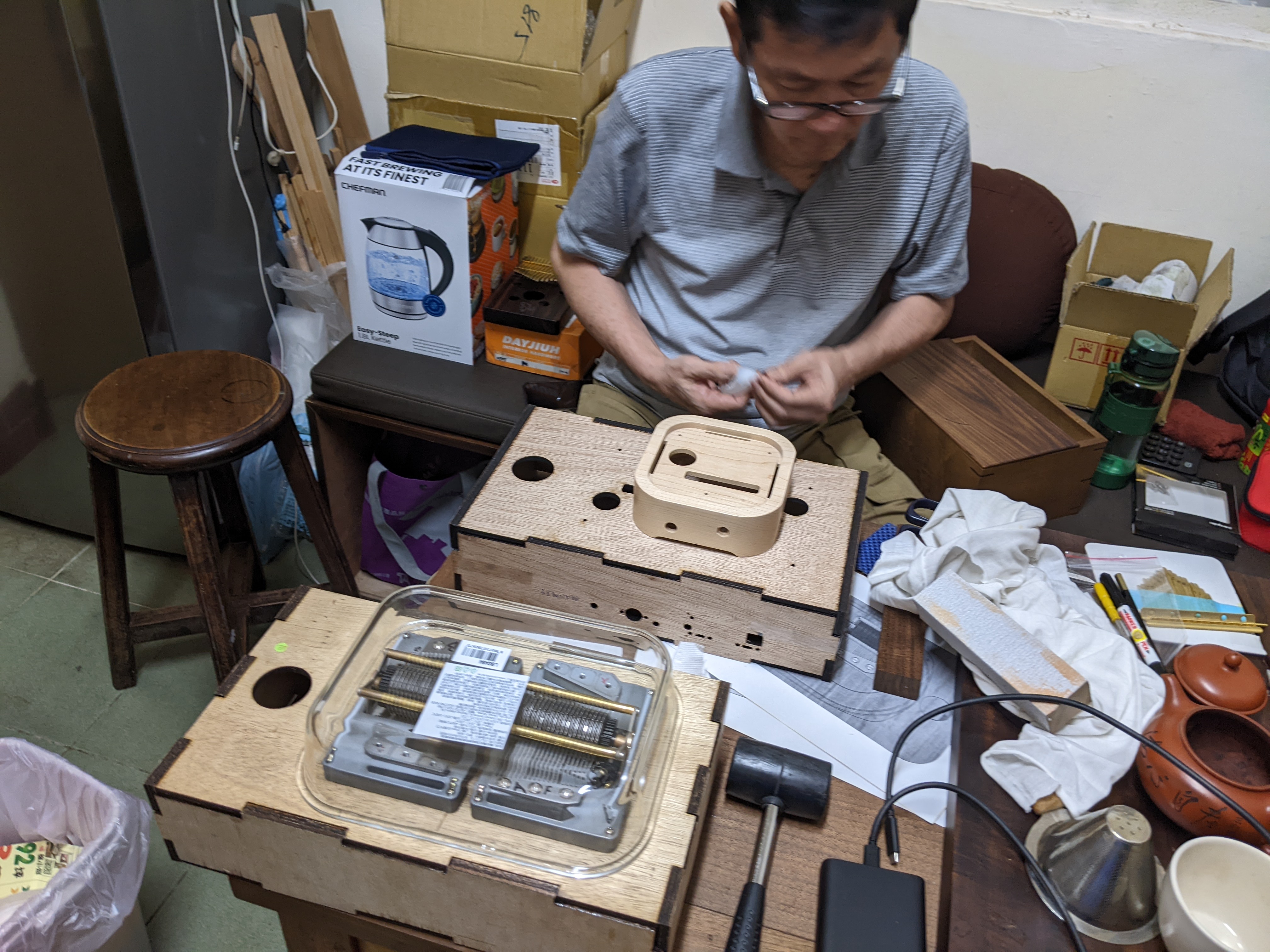
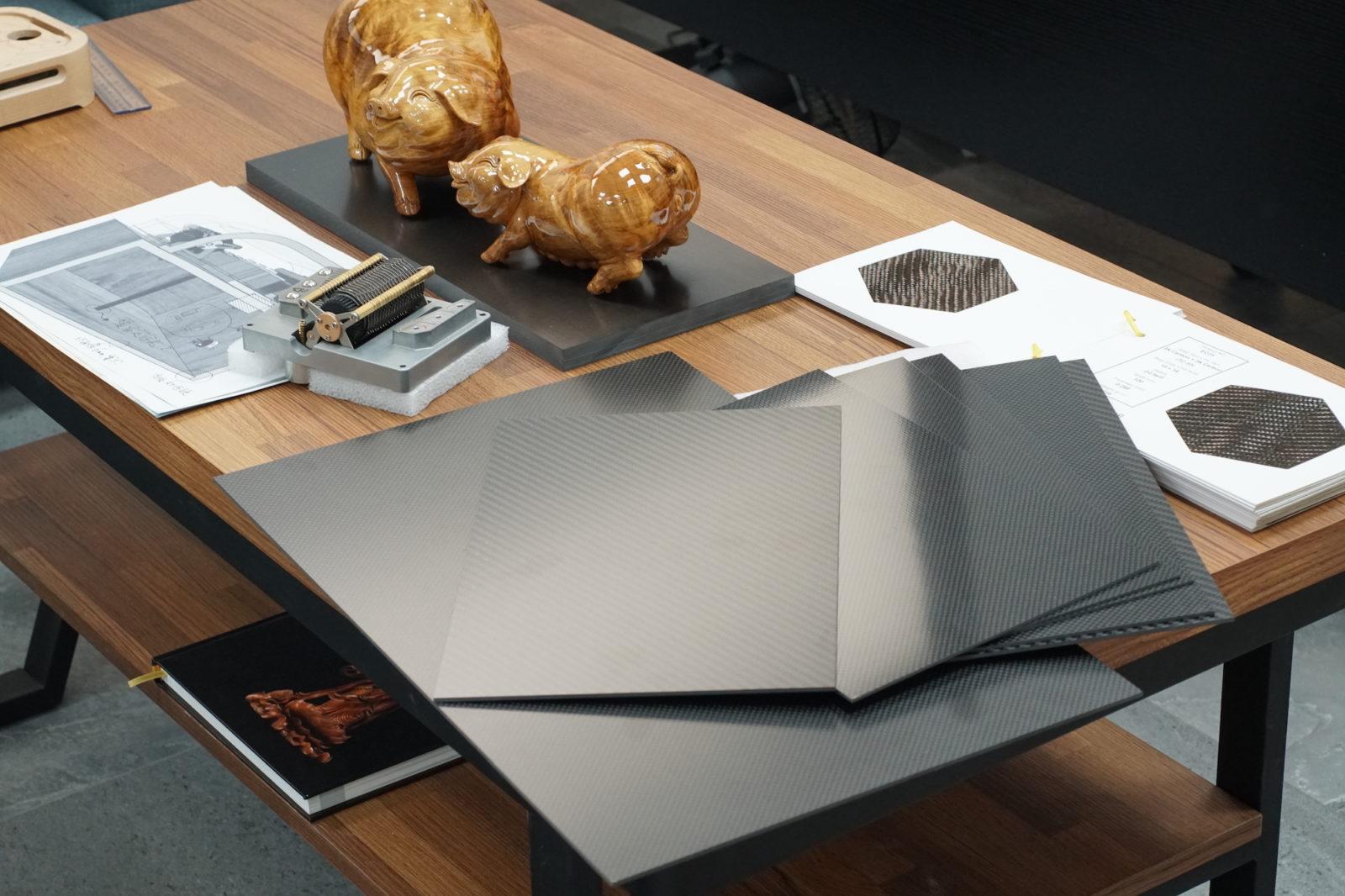
But in the end, none of these production methods were adopted. Aside from the difficulty in reaching a consensus on the aesthetic preferences for the wood box, the main consideration was the high cost of these tests—whether it was mold-making or purely manual labor, the costs were too high. Based on the development experience of the N20 music box, we knew there would be multiple design changes for N40 as well, so I had to choose the most flexible and reliable manufacturing method.
At the same time, I also had to resolve the issue of selecting the material for the wood box. During the pandemic, global shipping was chaotic, and the common woods used for music boxes were all imported, with prices soaring and unstable availability. As a result, purchasing the suitable solid wood caused me a great deal of stress. It was at this point that a foreign customer’s survey response caught my attention: “I see you discussing Western woods—have you considered using local Taiwanese woods?”
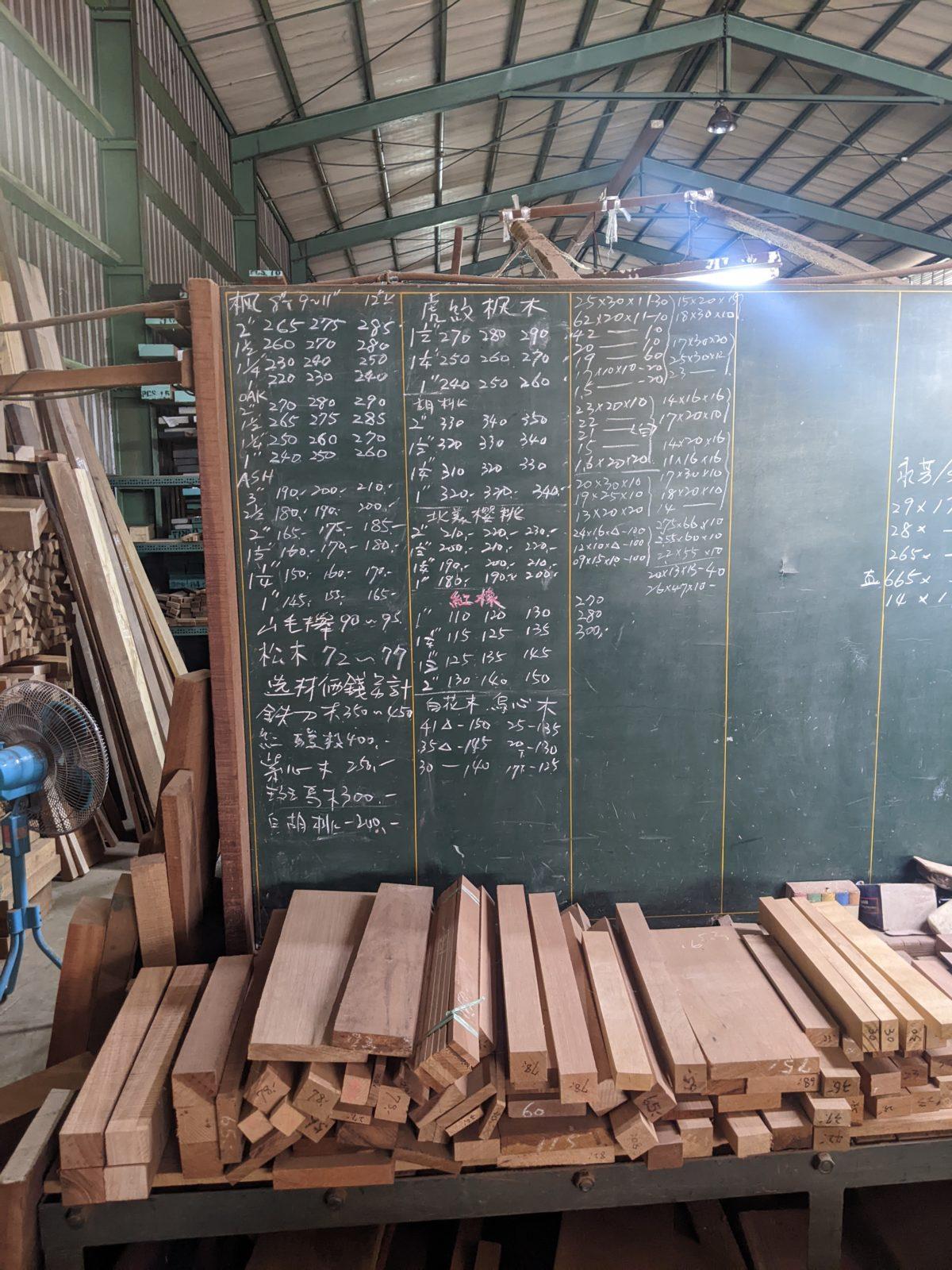
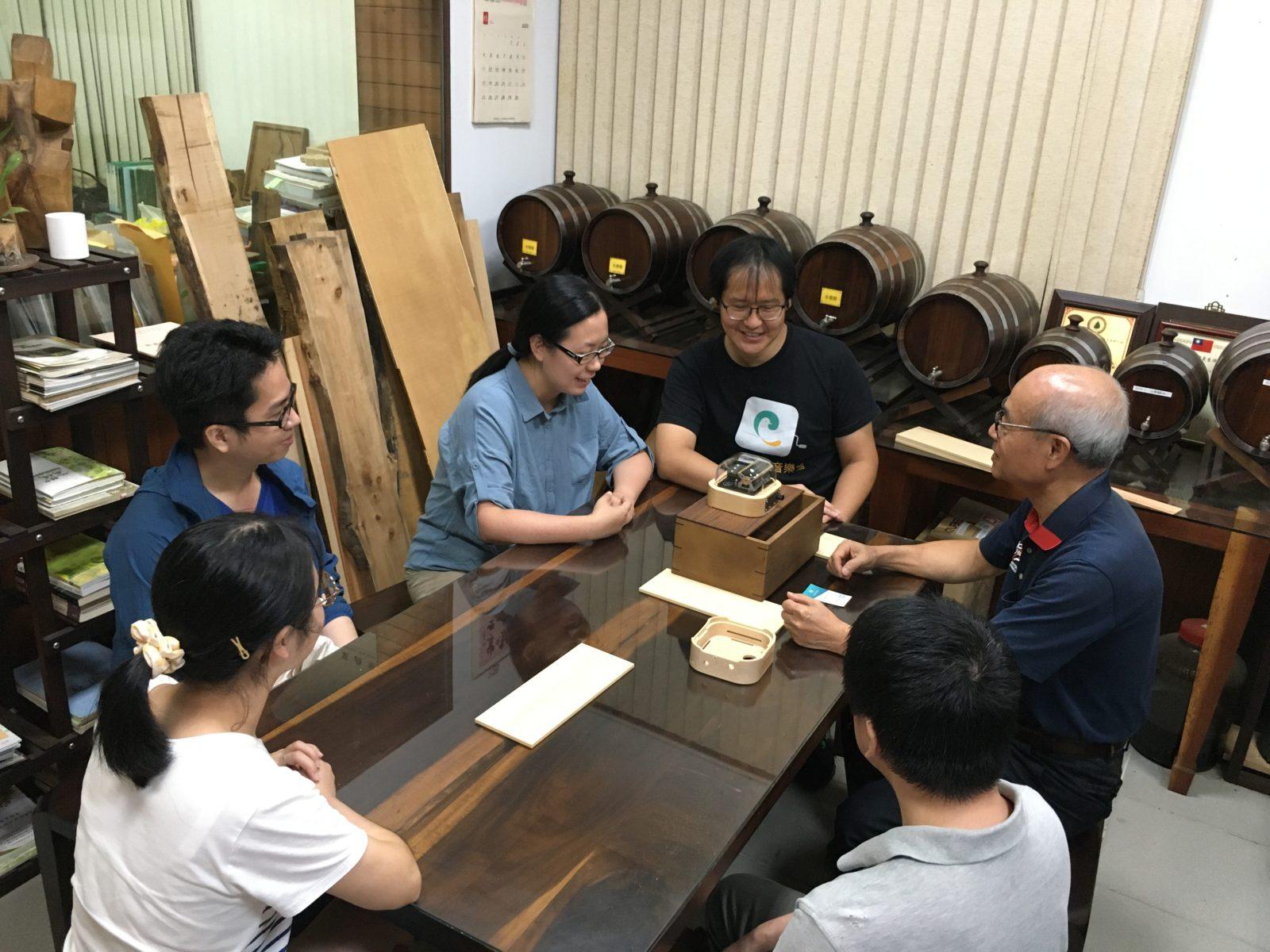
His suggestion was a wake-up call—I’d completely forgotten the simple principle of using local materials. Through a friend’s referral, we went to Yilan to find a supplier of Taiwan’s native Acacia wood, and through them, we were introduced to a CNC machining factory in Taipei. Finally, we were able to complete the design of the wood box.
Welcome to read the complete development journey of the wood box of Muro Box music boxes:
Production Challenges
In fact, we initially thought there would be no issues with producing the N40. We had been producing the N20 steadily for so long, and the vibration plate had even passed the N40 test before the project began. However, we never expected that we would still end up facing delays in delivery. We underestimated the severity of the design changes, but if we didn’t make adjustments, we couldn’t improve the quality—it was truly a dilemma.
Looking at it now, launching the N40 through crowdfunding was the right decision. The supporters of crowdfunding can understand that the product is still in the development stage, and they are patient enough to wait for us. Thank you very much for your support.
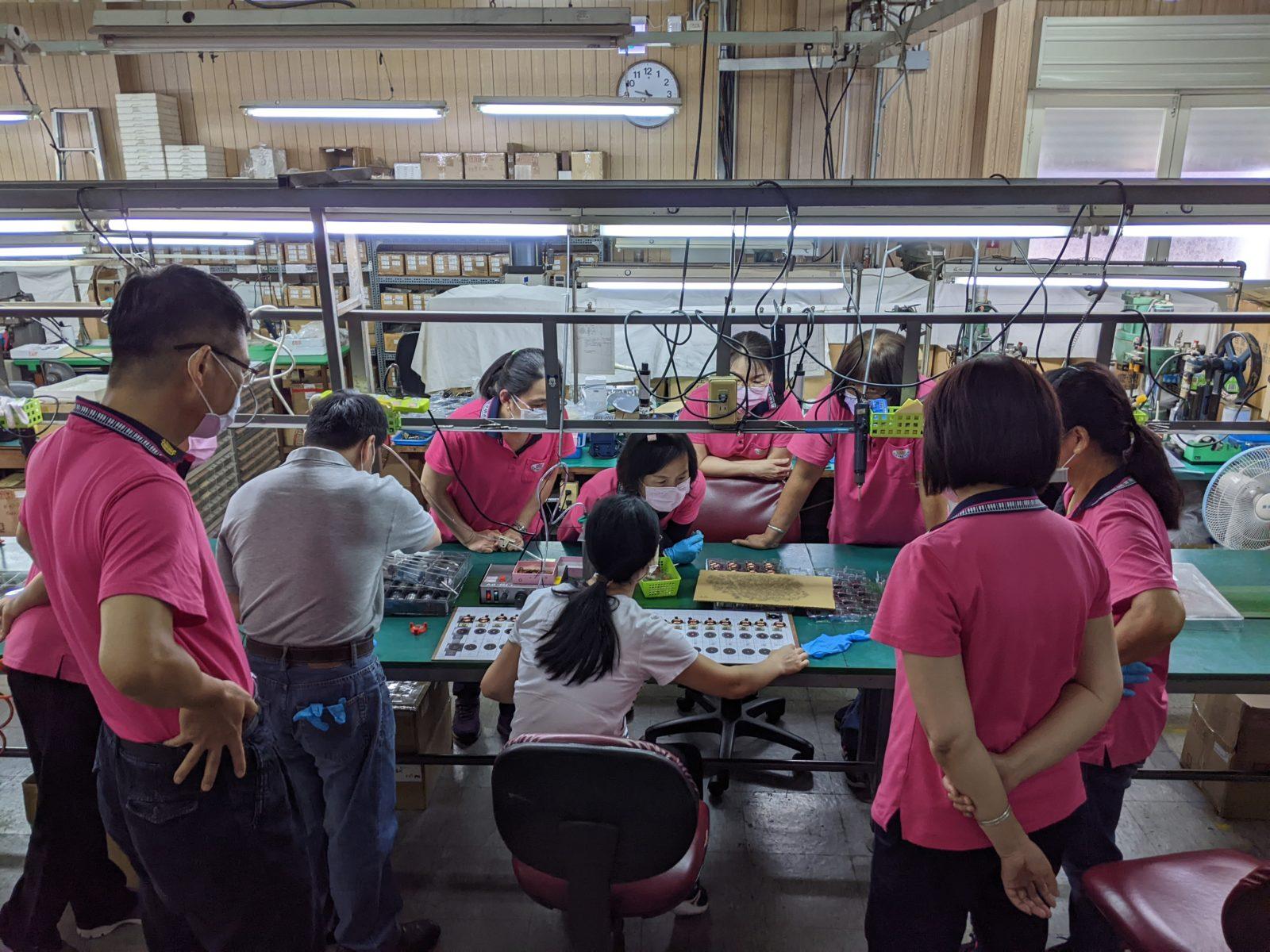
But the real reason for the difficulties we faced with shipments was that shortly after the 2023 Kickstarter crowdfunding campaign went live, I was diagnosed with colorectal cancer. It all started when I noticed blood in my stool, so I underwent a colonoscopy and discovered a tumor. Initially, I thought the tumor appeared normal, which led me to believe it was an early-stage, non-severe condition (I was 42 years old). However, after surgery to remove the tumor, I was informed that it was stage III cancer and had already spread to multiple lymph nodes. As soon as my wound healed, I began chemotherapy.
I’m sure most of you know someone who has undergone chemotherapy and have a general idea of the side effects. To put it simply, the cancer itself didn’t cause me much pain, but chemotherapy truly made me suffer a lot. Numbness in my hands and feet, vomiting, and whole-body allergic reactions were my everyday challenges. The biggest psychological pressure came from knowing that once that injection was given, my entire body would react abnormally. Not only did I have to receive the injection every few weeks, but I also had to stay in the hospital for continuous three-day IV drips. In the end, just smelling the disinfectant in the hospital would make me nauseous. I can fully understand why some people might want to give up on treatment.
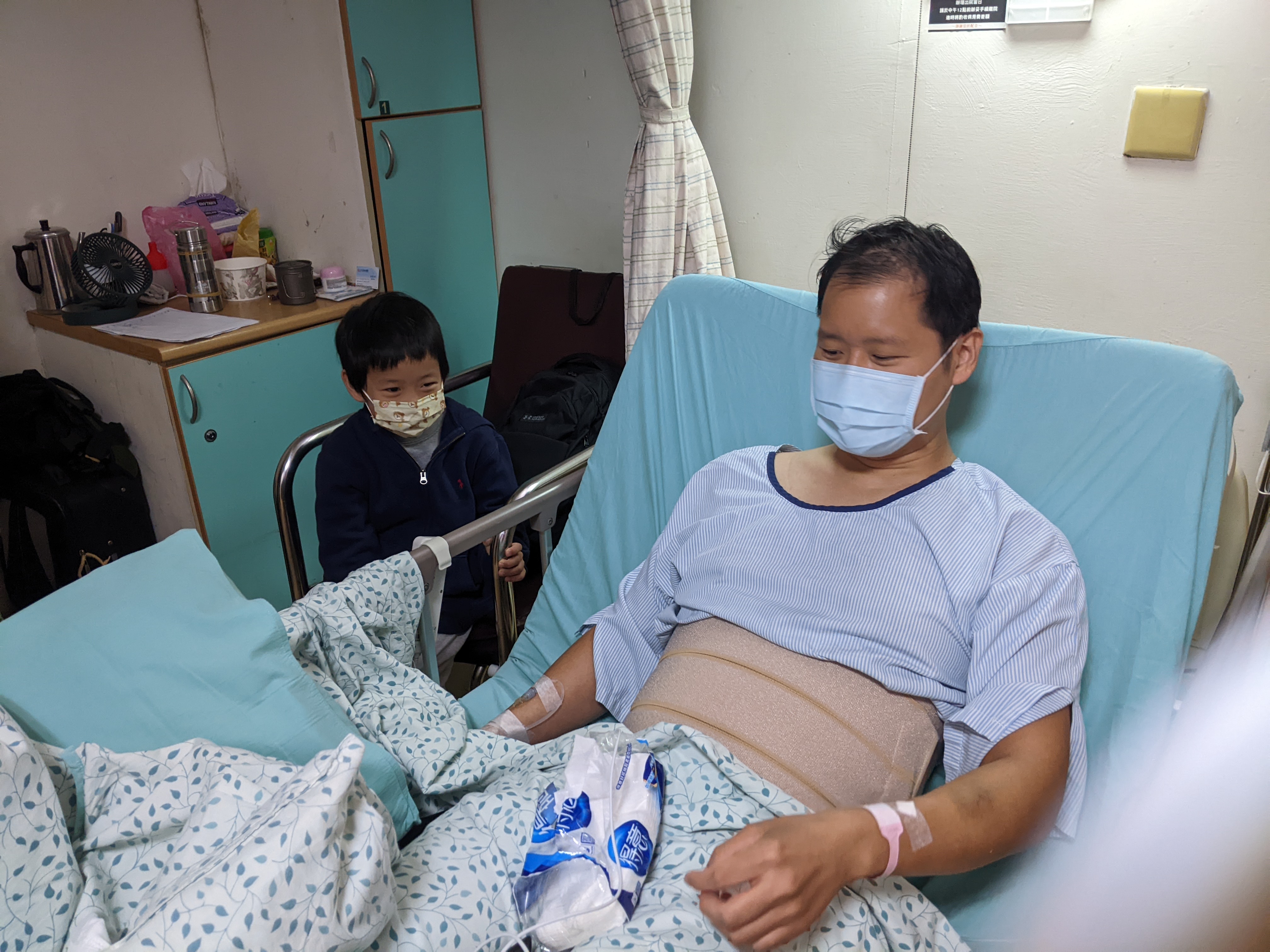

Therefore, this incident did affect the progress of the N40 music box. After all, there were times when I had to go to the hospital for treatment. Unfortunately, the timing of my chemotherapy overlapped with the N40’s shipping schedule, and there were moments when I came back from chemotherapy and went straight to the office to work on the project. However, I’m relieved to say that after finishing chemotherapy, the full-body checkups showed no signs of cancer cells. I can’t say I’m completely recovered, but it’s certain that there are no issues in the next few years, so please don’t worry.
Where did the N20 Battery model go?
We’ve received quite a few inquiries asking why the battery model suddenly disappeared. The truth is, at the beginning, we did plan to launch the battery model project once the total crowdfunding amount reached a certain level. However, shortly after, my health issues were discovered, and in the midst of struggling to manage everything, the N20 battery model naturally had to be put on hold.

Since we continued to receive occasional requests from customers for a battery-powered version, we never gave up on the idea of the N20 Battery Edition. After multiple design revisions and the development of new features, we eventually renamed it N20 Lite Go and launched a crowdfunding campaign for it on Wabay in May 2025.
As you may already know, the N20 Lite Go campaign was terminated early—just 11 days after its relaunch. In short, the demand for a battery-powered version proved to be too niche, making it unsuitable for a crowdfunding approach.
You can read more about the details in the development story of the N20 Lite Go.
What's Next
The birth of N40 is a milestone for us. On the engineering side, we have gained a deeper understanding of more core technologies. On the business side, we’ve expanded our audience, and in terms of branding, we’ve established our own style and are no longer blindly following others.
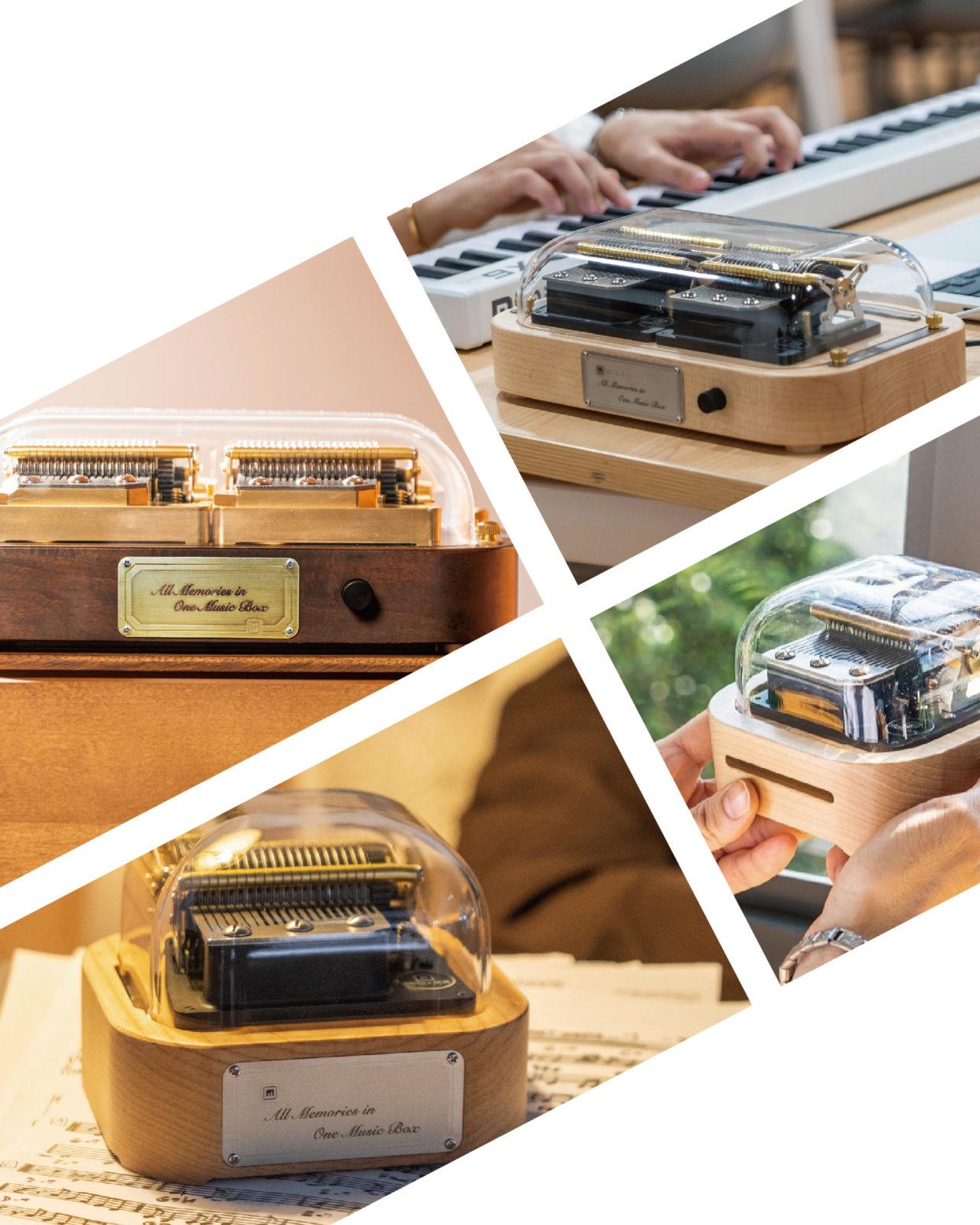
We now have four models of music boxes:
N20 Lite: A customized melody/laser-engraved music box, perfect for presenting a meaningful gift for someone special.
N20 Standard: A music instrument for experiencing the joy of melody composition, suitable for gift preparation as well as self use.
N40 Standard: An automatic instrument suitable for melody composition enthusiasts
N40 Sublime: A masterpiece for enriching your craftsmanship collection
Welcome to explore: Which Music Box Is Suitable for Me?, Muro Box-Music Box Gift Guide, and How to Unleash Your Creativity in Arranging Music Box Melodies to help you choose the model that best suits you.
We will continue to expand the technological advantages of our music boxes and launch even more innovative and refined models. We hope you’ll join us in keeping the magic of music boxes alive for generations to come.
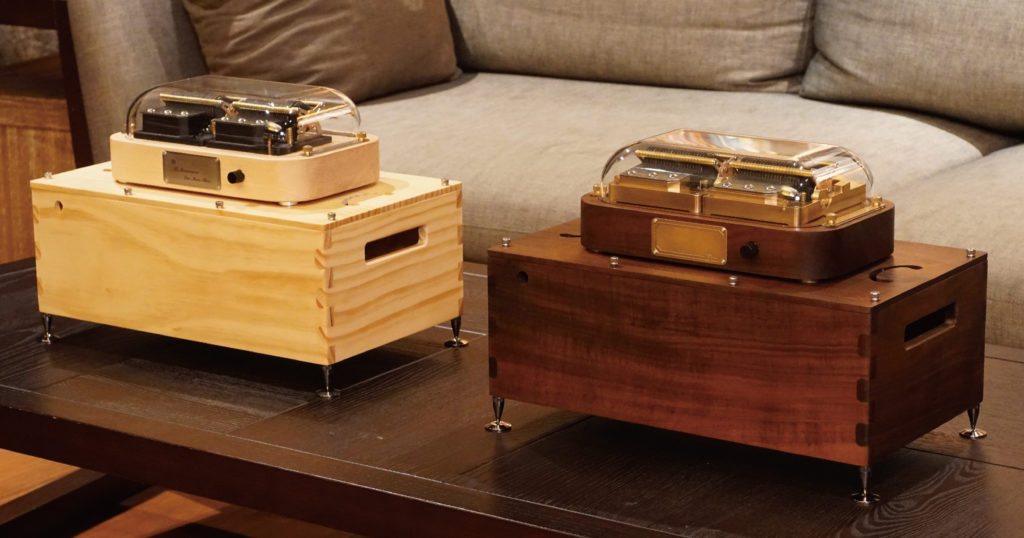